Tube-wound heat exchanger with separated core and shell
A technology of wound-tube heat exchangers and core shells, applied in indirect heat exchangers, heat exchanger types, heat exchanger shells, etc., can solve the problems of traditional structures that are difficult to process and manufacture, so as to prevent pipe rupture and improve design The effect of precision
- Summary
- Abstract
- Description
- Claims
- Application Information
AI Technical Summary
Problems solved by technology
Method used
Image
Examples
Embodiment 1
[0024] Such as figure 2 with image 3 As shown, this embodiment includes a central cylinder 4, a groove-type homogenizer 5, and an annular sealing section 7 arranged in the housing. The central cylinder 4 is arranged in the housing 2 to form an annular cavity between the two. The distributor 5 is nested in the housing 2 and sleeved on the central cylinder 4, the annular sealing section 7 is nested in the housing 2 and connected to the bottom of the homogenizer 5, and the sleeve 3 is disposed in the annular cavity and sleeved On the annular sealing section 7;
[0025] Such as image 3 with Figure 4 As shown, the bottom plate of the homogenizer 5 is symmetrically provided with two gas phase circulation holes 9 near the edge, and the bottom plate of the homogenizer 5 is uniformly distributed with a plurality of liquid phase circulation holes 8 except for the gas phase circulation holes 9.
[0026] The diameter of the liquid phase circulation hole 8 is 0.2 mm-2 mm; the gas phase circul
PUM
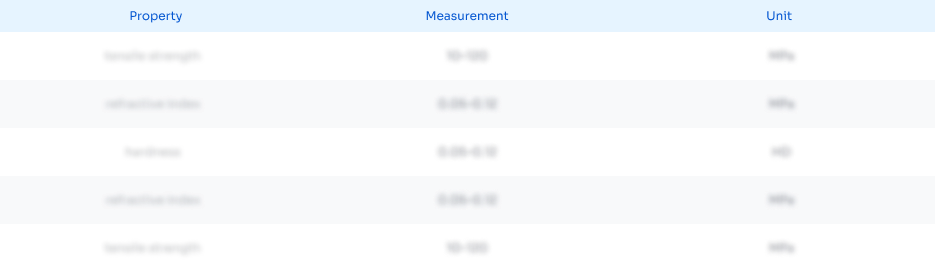
Abstract
Description
Claims
Application Information
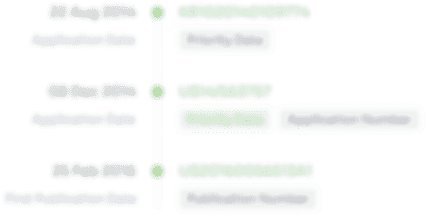
- R&D Engineer
- R&D Manager
- IP Professional
- Industry Leading Data Capabilities
- Powerful AI technology
- Patent DNA Extraction
Browse by: Latest US Patents, China's latest patents, Technical Efficacy Thesaurus, Application Domain, Technology Topic.
© 2024 PatSnap. All rights reserved.Legal|Privacy policy|Modern Slavery Act Transparency Statement|Sitemap