Drive device for twin-screw extruder
A twin-screw extruder and driving device technology, which is applied in the direction of mechanical equipment, bearings, liquid cushion bearings, etc., can solve problems such as inapplicability, and achieve the effect of increasing life and shortening length
- Summary
- Abstract
- Description
- Claims
- Application Information
AI Technical Summary
Benefits of technology
Problems solved by technology
Method used
Image
Examples
Embodiment Construction
[0018] The invention relates to a drive for a twin-screw extruder. The construction of drives for twin-screw extruders is well known to those skilled in the art mentioned here and is known from DE 10 2004 051 306 B4. Accordingly, the drive means for the twin-screw extruder comprises at least one electric motor 16, 16', 30, wherein each motor acts on a drive or input shaft 17, 25, 37. Furthermore, the drive of the twin-screw extruder comprises a plurality of output shafts 60 , 84 , wherein the screw shaft 2 , 4 of the twin-screw extruder is coupled to each drive shaft 60 , 84 .
[0019] A planetary gear assembly 8 with at least one planetary gear stage and a gear assembly configured as a power split transmission 10 is connected between the or each drive or input shaft 17 , 25 , 37 and the output shaft 60 , 84 .
[0020] The invention concerns these details of the drive for a twin-screw extruder, with which an advantageous axial support of the two output shafts 60 , 84 of the
PUM
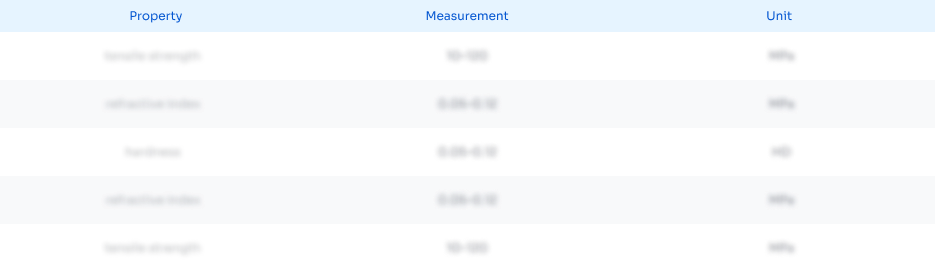
Abstract
Description
Claims
Application Information
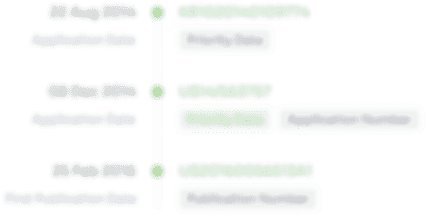
- R&D Engineer
- R&D Manager
- IP Professional
- Industry Leading Data Capabilities
- Powerful AI technology
- Patent DNA Extraction
Browse by: Latest US Patents, China's latest patents, Technical Efficacy Thesaurus, Application Domain, Technology Topic.
© 2024 PatSnap. All rights reserved.Legal|Privacy policy|Modern Slavery Act Transparency Statement|Sitemap