Pouring base plate
A chassis and sliding plate technology, which is applied in the field of metallurgical casting, can solve the problems such as inconvenient detachment of steel ingots, and the inability to adjust the pouring flow, and achieve the effects of unpacking cleaning and transfer operations, shortening demoulding time and efficiency, and improving the quality of steel ingots
- Summary
- Abstract
- Description
- Claims
- Application Information
AI Technical Summary
Problems solved by technology
Method used
Image
Examples
Embodiment Construction
[0046] The above-mentioned technical features and advantages of the present invention will be clearly and completely described below in conjunction with the accompanying drawings. Apparently, the described embodiments are only some, not all, embodiments of the present invention.
[0047] see figure 1 As shown, the present invention proposes a pouring chassis, which includes a body 10 and a flow control and cutting device. An accommodation cavity 14 is provided inside the body 10 , and flow steel brick holes 12 extending to the upper surface of the body 10 are opened on the body 10 , and the flow steel brick holes 12 communicate with the accommodation cavity 14 .
[0048] The flow control and cutting device includes a flow steel brick 22 , a sliding plate 24 capable of sliding horizontally, a drainage body 26 and a push rod 28 capable of pushing and pulling in the radial direction of the sliding plate 24 . The flow steel brick 22 has a through flow hole 222 , the sliding plate 24
PUM
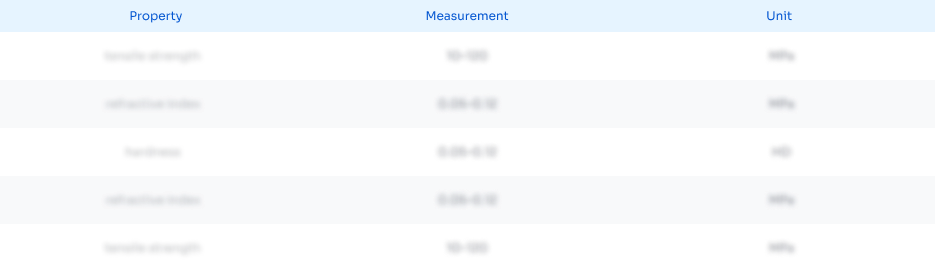
Abstract
Description
Claims
Application Information
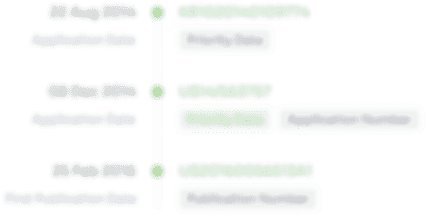
- R&D Engineer
- R&D Manager
- IP Professional
- Industry Leading Data Capabilities
- Powerful AI technology
- Patent DNA Extraction
Browse by: Latest US Patents, China's latest patents, Technical Efficacy Thesaurus, Application Domain, Technology Topic.
© 2024 PatSnap. All rights reserved.Legal|Privacy policy|Modern Slavery Act Transparency Statement|Sitemap