Front longitudinal beam structure
A front longitudinal beam and reinforcing structure technology, which is applied in the substructure, transportation and packaging, vehicle parts, etc., can solve the problems of high input cost in the manufacture of molds and fixtures, unfavorable lightweight development, and many stamping and forming processes. Conducive to lightweight design, saving manufacturing cost and low mold cost
- Summary
- Abstract
- Description
- Claims
- Application Information
AI Technical Summary
Benefits of technology
Problems solved by technology
Method used
Image
Examples
Embodiment Construction
[0028] The technical solutions of the present invention will be further described below in conjunction with the accompanying drawings and through specific implementation methods.
[0029] Such as Figures 1 to 2 As shown, a front longitudinal beam structure includes: a first connecting beam 10 and a second connecting beam 20 arranged longitudinally, and a cross beam 30, and the opposite ends of the first connecting beam 10 and the second connecting beam 20 are connected by a connecting plate 41 One end of the crossbeam 30 is welded to the end of the first connecting beam 10; the connection of the first connecting beam 10, the second connecting beam 20 and the crossbeam 30 is connected with a reinforcement structure, and the structural strength of the connection is improved by the reinforcement structure .
[0030] Specifically, the reinforcement structure includes reinforcing ribs 50 vertically welded to the second connecting beam 20 and the connecting plate 41 , and vertically
PUM
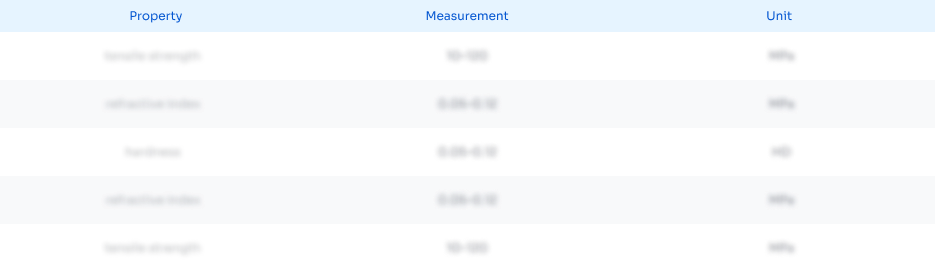
Abstract
Description
Claims
Application Information
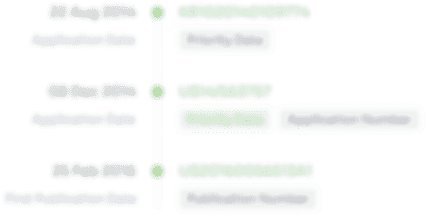
- R&D Engineer
- R&D Manager
- IP Professional
- Industry Leading Data Capabilities
- Powerful AI technology
- Patent DNA Extraction
Browse by: Latest US Patents, China's latest patents, Technical Efficacy Thesaurus, Application Domain, Technology Topic.
© 2024 PatSnap. All rights reserved.Legal|Privacy policy|Modern Slavery Act Transparency Statement|Sitemap