Preparation method of m-aminobenzole
A technology for aminoanisole and nitroanisole is applied in the field of preparation of m-aminoanisole, and can solve the problems of low production capacity, environmental pollution, low catalyst recycling rate and the like
- Summary
- Abstract
- Description
- Claims
- Application Information
AI Technical Summary
Problems solved by technology
Method used
Image
Examples
Embodiment 1
[0094] A kind of preparation method of m-aminoanisole, take m-nitroanisole as raw material, adopt Pd / Al 2 o 3 Catalyst, continuous catalytic hydrogenation reaction is carried out in the reactor, after the catalyst is separated and recovered, the reducing solution is desolvated and purified to obtain the target product m-aminoanisole.
[0095] Specific steps include:
[0096] (1) Put 5000kg of methanol and 1250kg of m-nitroanisole into the chemical tank, follow-up feeding according to this ratio, stir evenly, pump into the first-stage hydrogenation reactor, and add Pd / Al 2 o 3 Catalyst 125kg, the particle size of the catalyst is 10nm; pass through the nitrogen replacement system three times, then pass through the hydrogen replacement system three times, start stirring, raise the temperature to 90-100°C, and pump it into the first-stage hydrogenation tank at a flow rate of 6000L / h The raw material solution of m-nitroanisole is passed into H 2 , control the hydrogen pressu
Embodiment 2
[0100] (1) Put 5000kg of methanol and 1250kg of m-nitroanisole into the chemical material tank, and follow up the feeding according to the ratio, stir evenly, pump them into the first-stage hydrogenation reactor, and add Pd / Al 2 o 3 Catalyst 125kg, the particle size of the catalyst is 500μm; pass through the nitrogen replacement system three times, then pass through the hydrogen replacement system three times, start stirring, raise the temperature to 80-90°C, and pump it into the first-stage hydrogenation tank at a flow rate of 15000L / h The raw material solution of m-nitroanisole is passed into H 2 , control the hydrogen pressure in the system to 3.0MPa, and add Pd / Al to the primary hydrogenation reactor every 3h 2 o 3 Catalyst 2.5kg, after the material in the primary hydrogenation tank gradually increases, it flows into the secondary hydrogenation tank through the overflow port, and the material stays in the hydrogenation tank for about 2 to 3 hours. Residual amount of
Embodiment 3
[0104] (1) 12,500kg of methanol and 1,250kg of m-nitroanisole were put into the chemical tank, and the subsequent feeding was stirred evenly according to the ratio, pumped into the first-stage hydrogenation reactor, and Pd / Al was added 2 o 3 Catalyst 125kg, the particle size of the catalyst is 10nm; pass through the nitrogen replacement system three times, then pass through the hydrogen replacement system three times, start stirring, raise the temperature to 90-100°C, and pump it into the first-stage hydrogenation tank at a flow rate of 6000L / h The raw material solution of m-nitroanisole is passed into H 2 , control the hydrogen pressure in the system to 3.0MPa, and add Pd / Al to the primary hydrogenation reactor every 3h 2 o 3 Catalyst 2.5kg, after the material in the primary hydrogenation tank gradually increases, it flows into the secondary hydrogenation tank through the overflow port, and the material stays in the hydrogenation tank for about 2 to 2.5 hours. Anisole r
PUM
Property | Measurement | Unit |
---|---|---|
Average pore size | aaaaa | aaaaa |
Particle size | aaaaa | aaaaa |
Average pore size | aaaaa | aaaaa |
Abstract
Description
Claims
Application Information
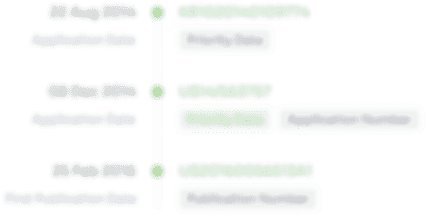
- R&D Engineer
- R&D Manager
- IP Professional
- Industry Leading Data Capabilities
- Powerful AI technology
- Patent DNA Extraction
Browse by: Latest US Patents, China's latest patents, Technical Efficacy Thesaurus, Application Domain, Technology Topic.
© 2024 PatSnap. All rights reserved.Legal|Privacy policy|Modern Slavery Act Transparency Statement|Sitemap