Method for determining thicknesses of gaskets for assembling roll to bearing pedestal
A method for determining bearing housings, which is applied to the rigid support of bearing components, bearing elements, shafts and bearings, etc., can solve the problems of low efficiency, unsafe and cumbersome bearing housing components and rolls, etc., and achieve simplified assembly steps, The effect of reducing repeated hoisting and improving assembly efficiency
- Summary
- Abstract
- Description
- Claims
- Application Information
AI Technical Summary
Problems solved by technology
Method used
Examples
Example Embodiment
[0019] Example
[0020] A cold-rolled galvanizing line wet finishing machine is a single-stand four-high rolling mill, and the bearing adopts single-stand galvanized finishing machine bearings. The radial and axial spacers are determined as follows:
[0021] The axial gap G given in the design is 0.2~0.4, and the intermediate value 0.3 is used in the calculation. The range of λ is 0.063~0.12 after calculation and statistics, and the unit of all involved values is mm.
[0022] (1) Assemble the lower box on the operating side of the support roller
[0023] Box No.: 23569090 2#013-2
[0024] Rack position: under the operating side
[0025] Roll number: B04-006
[0026] Bearing number: CZ2641461-004
[0027] Original width of bearing inner ring: 480.135
[0028] a. Assemble the bearing in the bearing housing, install the bearing gland, and use the "finger tight" method to tighten the bolts.
[0029] b. Measure the distance between the gland and the end face of the bearing seat, measuring 6 points
PUM
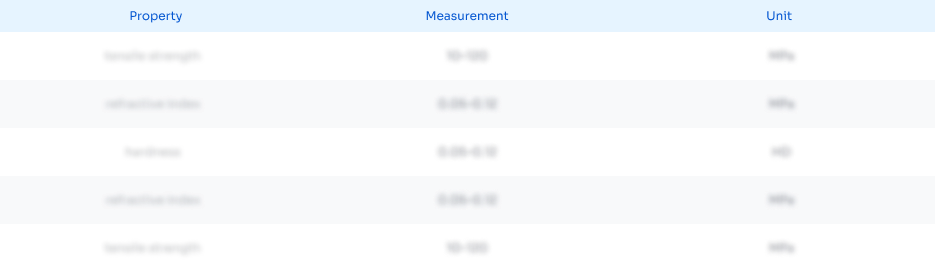
Abstract
Description
Claims
Application Information
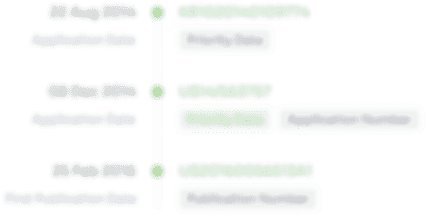
- R&D Engineer
- R&D Manager
- IP Professional
- Industry Leading Data Capabilities
- Powerful AI technology
- Patent DNA Extraction
Browse by: Latest US Patents, China's latest patents, Technical Efficacy Thesaurus, Application Domain, Technology Topic.
© 2024 PatSnap. All rights reserved.Legal|Privacy policy|Modern Slavery Act Transparency Statement|Sitemap