Method for measuring physical yielding point position and stress level of component
A technology of stress level and measurement method, applied in the direction of applying stable tension/pressure to test the strength of materials, measuring devices, instruments, etc., can solve the problem that the performance of component points is difficult to give detailed results, so as to improve the overall performance, Good practicality, easy to use effect
- Summary
- Abstract
- Description
- Claims
- Application Information
AI Technical Summary
Problems solved by technology
Method used
Examples
Example Embodiment
[0031] Example 1
[0032] A method for determining the physical yield point position and stress level of a member. In the process of static load tensile test, infrared thermal imaging of the member is taken, and based on the synchronized load and member temperature field data, the physical yield point position and stress level of the thin plate member are determined. Stress levels are accurately measured.
[0033] Further, the first step is to design and manufacture the components. In addition to the national standards, the component design should also reduce heat loss, such as using hole components to reduce the heat loss caused by clamping; the second step, in the static load tension The conventional tensile test is carried out on the tensile machine, and the infrared thermal image of the component is photographed and recorded during the whole test process, and the shooting speed is higher than the sampling speed selected for the static load tensile test; the third step is base
Example Embodiment
[0036] Example 2
[0037] A method for determining the physical yield point position and stress level of a member. In the process of static load tensile test, infrared thermal imaging of the member is taken, and based on the synchronized load and member temperature field data, the physical yield point position and stress level of the thin plate member are determined. Stress levels are accurately measured.
[0038]Further, the first step is to design and manufacture the components. In addition to the national standards, the component design should also reduce heat loss, such as using hole components to reduce the heat loss caused by clamping; the second step, in the static load tension The conventional tensile test is carried out on the tensile machine, and the infrared thermal image of the component is photographed and recorded during the whole test process, and the shooting speed is higher than the sampling speed selected for the static load tensile test; the third step is based
PUM
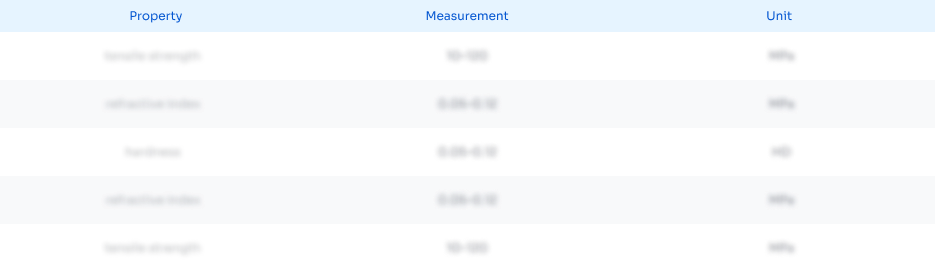
Abstract
Description
Claims
Application Information
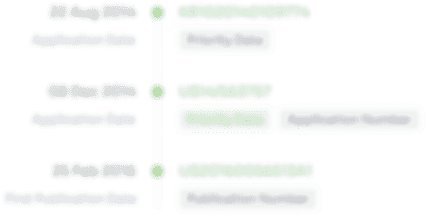
- R&D Engineer
- R&D Manager
- IP Professional
- Industry Leading Data Capabilities
- Powerful AI technology
- Patent DNA Extraction
Browse by: Latest US Patents, China's latest patents, Technical Efficacy Thesaurus, Application Domain, Technology Topic.
© 2024 PatSnap. All rights reserved.Legal|Privacy policy|Modern Slavery Act Transparency Statement|Sitemap