Aluminum shell bearing seat thermal-mechanical coupling strain measurement system and measurement method
A thermal-mechanical coupling and strain measurement technology, applied in the direction of electric/magnetic solid deformation measurement, measuring devices, electromagnetic measuring devices, etc., can solve problems such as shell damage, bearing failure, loose fit between shell and bearing outer ring, etc., to achieve guaranteed The effect of accuracy
- Summary
- Abstract
- Description
- Claims
- Application Information
AI Technical Summary
Problems solved by technology
Method used
Image
Examples
Embodiment 1
[0032] This embodiment provides a thermomechanical coupling strain measurement system for an aluminum housing bearing seat, which includes: a base 1, a dynamometer 2, a left drive shaft 3, a high and low temperature control box 4, a transition flange 5, a left support seat 6, The sample assembly 7 to be tested, the middle support seat 8 of the sample and the right drive shaft 9, and the static test assembly or the dynamic test assembly; The static test of the thermal-mechanical coupling strain of the bearing seat of the aluminum shell; when the thermal-mechanical coupling strain measurement system of the bearing seat of the aluminum shell includes a dynamic measurement component, the dynamic test of the thermal-mechanical coupling strain of the bearing seat of the aluminum shell can be realized.
[0033] The static test assembly includes a right support base 10 , a loading handle 11 , a lock 12 , a force sensor 13 , a D-shaped adjustment buckle 14 , a support base 15 and a support
Embodiment 2
[0051] This embodiment provides a thermal-mechanical coupling strain measurement method for an aluminum housing bearing seat, which uses the thermal-mechanical coupling strain measurement system for an aluminum housing bearing seat described in Embodiment 1, and the method includes:
[0052] S10, pasting the strain gauge and the temperature compensation sheet.
[0053] In this embodiment, the transmission assembly to be measured is disassembled, and the aluminum housing of the transmission assembly is simulated and calculated, and strain gauges are pasted on the maximum stress position of the bearing seat of the transmission assembly or the concerned part.
[0054] Among them, in the high-temperature thermal-mechanical coupling strain test, the resistance strain gauge is pasted at the end face of the bearing seat close to the bearing hole side, and a set of strain gauges is pasted on the theoretically loaded maximum stress of the front bearing seat and rear bearing seat of the tra
PUM
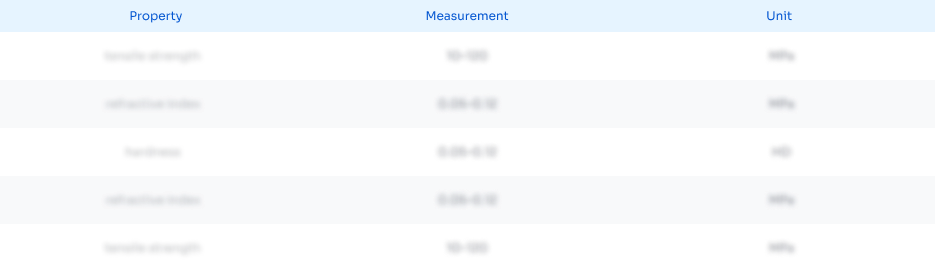
Abstract
Description
Claims
Application Information
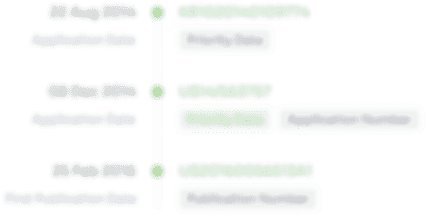
- R&D Engineer
- R&D Manager
- IP Professional
- Industry Leading Data Capabilities
- Powerful AI technology
- Patent DNA Extraction
Browse by: Latest US Patents, China's latest patents, Technical Efficacy Thesaurus, Application Domain, Technology Topic.
© 2024 PatSnap. All rights reserved.Legal|Privacy policy|Modern Slavery Act Transparency Statement|Sitemap