A manufacture method of U-shaped electric heating tube
A technology for electric heating tubes and production methods, applied in the direction of ohmic resistance heating components, heating elements, heating element shapes, etc., can solve the requirements of insulation, heat conduction, high temperature resistance, high voltage resistance, magnesium powder insulation structure It cannot adapt to the use requirements of electric heating tubes, high insulation layer requirements, etc., to achieve good filling effect, compact structure, and good support effect
- Summary
- Abstract
- Description
- Claims
- Application Information
AI Technical Summary
Problems solved by technology
Method used
Examples
Embodiment Construction
[0025] A production method of U-shaped electric heating tube includes the following steps:
[0026] In the first step, the magnesia raw material made by the thermal decomposition of hydrate is sintered to make a triangular prism magnesium tube; the magnesium oxide raw material made by the thermal decomposition of hydrate has good sintering performance, moisture resistance, high temperature resistance, excellent insulation performance, and good supporting effect;
[0027] The second step is to wind the resistance wire, connect the heat-conducting rod, pretreatment, and test; specifically include: selecting the resistance wire material, diameter and mandrel according to product specifications, design requirements, and customer use conditions. In this example, the material selected is nickel-chromium electric heating alloy ; Then wash and dry, you can soak in the detergent for 3-5 minutes, then knead, rinse, and dry at 120 ℃ for 30 minutes; after washing and drying, insert the thermal con
PUM
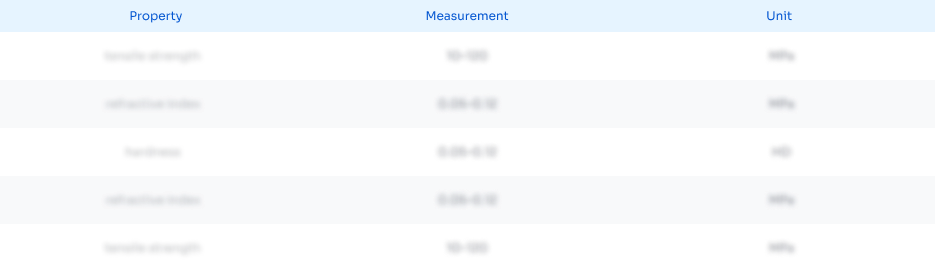
Abstract
Description
Claims
Application Information
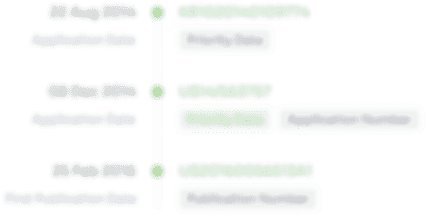
- R&D Engineer
- R&D Manager
- IP Professional
- Industry Leading Data Capabilities
- Powerful AI technology
- Patent DNA Extraction
Browse by: Latest US Patents, China's latest patents, Technical Efficacy Thesaurus, Application Domain, Technology Topic.
© 2024 PatSnap. All rights reserved.Legal|Privacy policy|Modern Slavery Act Transparency Statement|Sitemap