Silicone grease and preparation method thereof, and ink following agent using silicone grease, and preparation method thereof
A technology of silicone grease and ink, which is applied in chemical instruments and methods, and other chemical processes, can solve problems such as poor follow-up, low sealing, and poor low/high temperature resistance, achieving low cost, improved high temperature resistance, The effect of improved follow-up
- Summary
- Abstract
- Description
- Claims
- Application Information
AI Technical Summary
Problems solved by technology
Method used
Image
Examples
preparation example Construction
[0033] The present invention provides the preparation method of above-mentioned silicone grease again, comprises:
[0034] 25-30 parts by mass of butyl rubber, 25-30 parts by mass of phenyl silicone rubber, 5-15 parts by mass of base oil, 10-15 parts by mass of filling reinforcing agent and 1-5 parts by mass of structural After the chemical control agent is mixed, it is mixed in a mixer to form a mixed material;
[0035] The mixed material is ground by a three-roll mill, and the silicone grease is formed after the material is discharged through the grinding.
[0036] The rubber mixing process is divided into three stages, namely, roll wrapping, powder eating and mixing. When mixing silicone rubber, it is necessary to raise the temperature of the mixer in advance, and then add various rubbers and fillers according to the order of feeding. In some embodiments, after the temperature in the kneader is raised to 110°C-130°C, the above-mentioned components are mixed in proportion and p
Embodiment 1
[0051] (1) Preparation of silicone grease
[0052] In terms of parts by mass, mix 27 parts of butyl rubber, 17 parts of phenyl silicone rubber, 10 parts of fumed silica, and 10 parts of dimethyl silicone oil, wherein the Mooney viscosity of butyl rubber is 51 Pa·s, and phenyl silicone The phenyl content of the rubber is 7%. Raise the temperature of the mixer to 125°C, place the above-mentioned mixed components in the mixer and knead for 2 hours to obtain a uniform mixed material; the mixed material is ground by a three-roll mill, and the first two rollers are controlled to The roll temperature is between 100°C and 110°C, and the third roll temperature is between 40°C and 60°C. Grinding until the material body is uniform can be discharged, and the modified silicone grease is obtained after discharging. The test method refers to the standard GB / T 269 test method, and the cone penetration of the obtained silicone grease is 245.
[0053] (2) Preparation of ink follower
[0054]
Embodiment 2
[0057] (1) Preparation of silicone grease
[0058] In parts by mass, mix 25 parts of butyl rubber, 25 parts of phenyl silicone rubber, 10 parts of fumed silica, and 10 parts of dimethyl silicone oil, wherein the Mooney viscosity of butyl rubber is 51 Pa·s, and phenyl silicone The phenyl content of the rubber is 5%. Raise the temperature of the mixer to 125°C, place the above-mentioned mixed components in the mixer and knead for 2 hours to obtain a uniform mixed material; the mixed material is ground by a three-roll mill, and the first two rollers are controlled to The roll temperature is between 100°C and 110°C, and the third roll temperature is between 40°C and 60°C. Grinding until the material body is uniform can be discharged, and the modified silicone grease is obtained after discharging. The test method refers to the standard GB / T 269 test method, and the cone penetration of the obtained silicone grease is 276.
[0059] (2) Preparation of ink follower
[0060] In terms
PUM
Property | Measurement | Unit |
---|---|---|
Kinematic viscosity | aaaaa | aaaaa |
Kinematic viscosity | aaaaa | aaaaa |
Shear viscosity | aaaaa | aaaaa |
Abstract
Description
Claims
Application Information
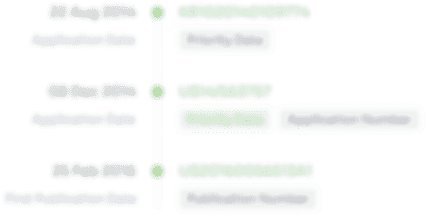
- R&D Engineer
- R&D Manager
- IP Professional
- Industry Leading Data Capabilities
- Powerful AI technology
- Patent DNA Extraction
Browse by: Latest US Patents, China's latest patents, Technical Efficacy Thesaurus, Application Domain, Technology Topic.
© 2024 PatSnap. All rights reserved.Legal|Privacy policy|Modern Slavery Act Transparency Statement|Sitemap