Preparation method of 1,8-naphthalic anhydride modified poly(propylene carbonate)
A technology of polypropylene carbonate and naphthalene anhydride, applied in 1 field, can solve the problems of low glass transition temperature, poor mechanical properties, increased flexibility, etc. Effect
- Summary
- Abstract
- Description
- Claims
- Application Information
AI Technical Summary
Benefits of technology
Problems solved by technology
Method used
Image
Examples
Embodiment 1
[0016] A 500mL high-pressure reactor was used as the reaction vessel, and the reactor was vacuum-dried at 80°C for 8 hours and purged with carbon dioxide. After cooling to room temperature, 1,8-naphthalene anhydride with a mass ratio of 0.6% was added, and the newly prepared rare earth three The primary catalyst and propylene oxide (PO), which accounted for 99.4% by mass, were filled with carbon dioxide, the pressure was kept at about 3.5MPa, the set temperature was 70°C, the speed was 250r / min, and the reaction was carried out for 10 hours. The reaction was stopped and the remaining gas was discharged. After the product was removed, it was washed with 5% hydrochloric acid ethanol solution to precipitate the polymer, washed 3 times with absolute ethanol, and vacuum-dried at 45°C to constant weight to obtain a copolymer.
Embodiment 2
[0018] A 500mL high-pressure reactor was used as the reaction vessel. The reactor was vacuum-dried at 80°C for 8 hours and purged with carbon dioxide. After cooling to room temperature, 1,8-naphthalene anhydride with a mass ratio of 1% was added, and the newly prepared rare earth three The primary catalyst and propylene oxide (PO), which accounted for 99% by mass, were charged with carbon dioxide, the pressure was kept at about 3.5MPa, the set temperature was 70°C, the speed was 250r / min, and the reaction was carried out for 10 hours. The reaction was stopped and the remaining gas was discharged. After the product was removed, it was washed with 5% hydrochloric acid ethanol solution to precipitate the polymer, washed 3 times with absolute ethanol, and vacuum-dried at 45°C to constant weight to obtain a copolymer.
Embodiment 3
[0020] A 500mL high-pressure reactor was used as the reaction vessel, and the reactor was vacuum-dried at 80°C for 8 hours and purged with carbon dioxide. After cooling to room temperature, 1,8-naphthalene anhydride with a mass ratio of 2% was added, and the newly prepared rare earth three The primary catalyst and propylene oxide (PO), which accounted for 98% by mass, were filled with carbon dioxide, the pressure was kept at about 3.5MPa, the set temperature was 70°C, the speed was 250r / min, and the reaction was carried out for 10 hours. The reaction was stopped and the remaining gas was discharged. After the product was removed, it was washed with 5% hydrochloric acid ethanol solution to precipitate the polymer, washed 3 times with absolute ethanol, and vacuum-dried at 45°C to constant weight to obtain a copolymer.
PUM
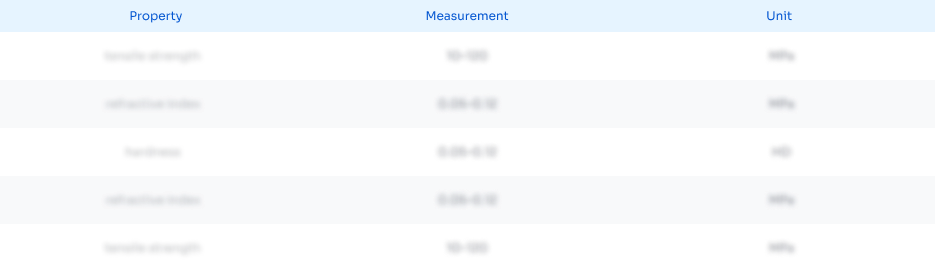
Abstract
Description
Claims
Application Information
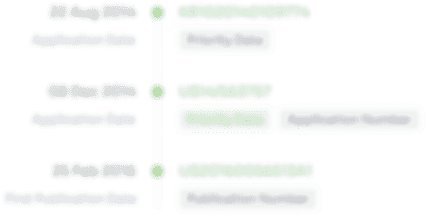
- R&D Engineer
- R&D Manager
- IP Professional
- Industry Leading Data Capabilities
- Powerful AI technology
- Patent DNA Extraction
Browse by: Latest US Patents, China's latest patents, Technical Efficacy Thesaurus, Application Domain, Technology Topic.
© 2024 PatSnap. All rights reserved.Legal|Privacy policy|Modern Slavery Act Transparency Statement|Sitemap