Resistive high-sensitivity flexible pressure sensor device
A pressure sensor, resistive technology, applied in the field of sensing devices, can solve the problems of limit output resistance reduction, sacrifice of measurement sensitivity, output mutation, etc.
- Summary
- Abstract
- Description
- Claims
- Application Information
AI Technical Summary
Benefits of technology
Problems solved by technology
Method used
Image
Examples
example 1
[0052] Such as Figure 1 to Figure 5 As shown, the circuit width in the ring electrode 5 is 0.5mm, the first central electrode circuit 12 and the second central electrode circuit 13 are concentric circular arcs with a radius of R1=2mm, the first central electrode circuit 12 and the second central electrode circuit 13 spacing D1=3mm, first outer ring electrode circuit 10 arc radius R2=3.5mm, second outer ring electrode circuit 11 arc radius R3=4.5mm, first center electrode circuit 12 and first outer ring electrode circuit The spacing D2 of 10 = 1 mm, and the spacing D3 = 0.5 mm between the first outer ring electrode circuit 10 and the second outer ring electrode circuit 11 . The length D4 of the first electrode lead-out end 8 and the second electrode lead-out end 9 is 3 mm, and the dimensions of the first test port 14 and the second test port 15 are D5 = 3.5 mm and D6 = 1.5 mm.
[0053] The inner ring pressure-sensitive layer 4 is a circular structure with a radius of R5=3.3mm, t
Embodiment 1
[0062] Implement the sensor performance test described in example 1:
[0063] Connect the first test port 14 and the second test port 15 in the prepared pressure sensor electrode to the processor module and the power supply module, and use the Japanese graphic high-speed recorder (GL900APS) to test its output under different pressure states voltage changes.
[0064] In this implementation example, the voltage provided to the sensor is 2.7V. When no external force acts on the surface of the sensor, the output voltage of the pressure sensor is 2.7V; when the applied external force is less than 20N, the output voltage of the pressure sensor is still about 2.7V without significant change. It is because the adhesive material used in packaging has a certain thickness, so that the pressure-sensitive layer and the electrode are separated by a certain distance in the initial state, so under a small external force, the pressure-sensitive layer and the electrode do not come into contact, an
PUM
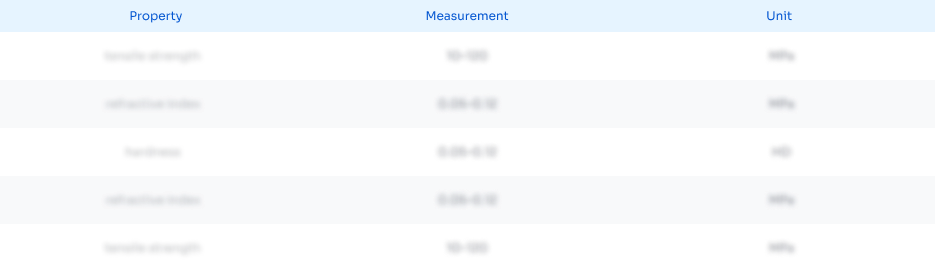
Abstract
Description
Claims
Application Information
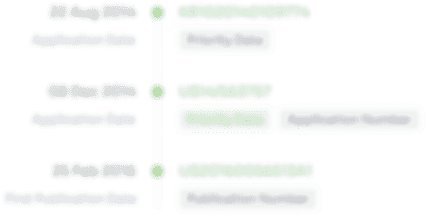
- R&D Engineer
- R&D Manager
- IP Professional
- Industry Leading Data Capabilities
- Powerful AI technology
- Patent DNA Extraction
Browse by: Latest US Patents, China's latest patents, Technical Efficacy Thesaurus, Application Domain, Technology Topic.
© 2024 PatSnap. All rights reserved.Legal|Privacy policy|Modern Slavery Act Transparency Statement|Sitemap