Blast furnace stockline descending top temperature controlling and detonation preventing method
A technology of empty material line and blast furnace, which is applied in the direction of blast furnace, blast furnace details, blast furnace parts, etc., can solve the problems that are not conducive to environmental protection and fail to achieve green production, and achieve improvement and reduction of furnace top temperature, good dilution effect, and shortened time Effect
- Summary
- Abstract
- Description
- Claims
- Application Information
AI Technical Summary
Benefits of technology
Problems solved by technology
Method used
Image
Examples
Embodiment 1
[0031] The method for controlling the top temperature of the blast furnace lowering line to prevent knocking, the specific implementation steps are as follows:
[0032] The effective volume of a blast furnace is 3200m 3 , In 2014, the empty material line was shut down for medium repair and the bosh stave was replaced.
[0033] (1) During the small wind break before the blast furnace shut down, remove the sprinkling device on the top of the furnace, install 8 purchased special atomizing water pumps, and install valves and flow meters, and then connect them to the industrial water pipe network. The maximum pumping capacity is 150t / h. In the process of emptying the material line, adjust the opening of the valve according to the actual temperature of the furnace top to control the amount of water drawn. The actual maximum pumping volume is 132t / h, and the top temperature is always within the required range.
[0034] (2) During the small wind break before the shutdown of the bl
Embodiment 2
[0037] A method for controlling top temperature and preventing detonation in a blast furnace lowering line. The specific implementation steps are as follows:
[0038] The effective volume of a blast furnace is 2600m 3 , In 2017, the empty material line was shut down for intermediate repairs to replace the bosh stave.
[0039] (1) During the small wind break before the blast furnace shut down, remove the sprinkling device on the top of the furnace, install 6 purchased special atomizing water pumps, and install valves and flow meters, and then connect them to the industrial water pipe network. The maximum pumping capacity is 130t / h. In the process of emptying the material line, adjust the opening of the valve according to the actual temperature of the furnace top to control the amount of water drawn. The actual maximum pumping volume is 115t / h, and the top temperature is always within the required range.
[0040] (2) During the small wind break before the shutdown of the blast
PUM
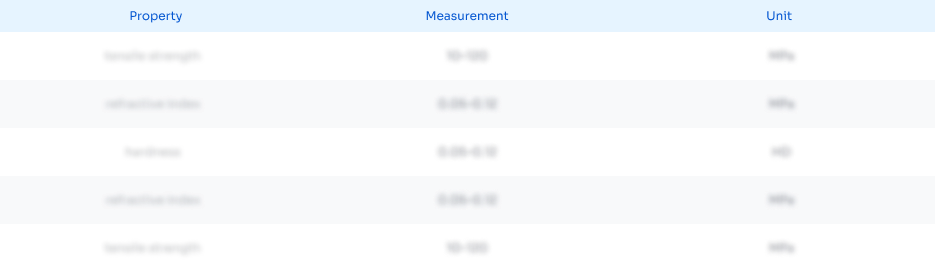
Abstract
Description
Claims
Application Information
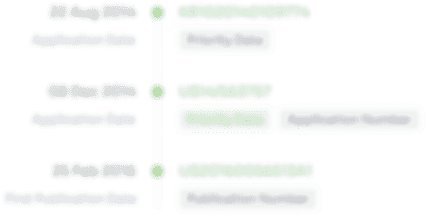
- R&D Engineer
- R&D Manager
- IP Professional
- Industry Leading Data Capabilities
- Powerful AI technology
- Patent DNA Extraction
Browse by: Latest US Patents, China's latest patents, Technical Efficacy Thesaurus, Application Domain, Technology Topic.
© 2024 PatSnap. All rights reserved.Legal|Privacy policy|Modern Slavery Act Transparency Statement|Sitemap