A space six-degree-of-freedom non-contact vibration isolation platform for aerospace
A vibration isolation platform and degree of freedom technology, applied in the field of aerospace systems, can solve the problems of limited low-frequency vibration isolation and complex structure, and achieve the effects of reduced accuracy requirements, simple structure and cost saving.
- Summary
- Abstract
- Description
- Claims
- Application Information
AI Technical Summary
Benefits of technology
Problems solved by technology
Method used
Image
Examples
Embodiment Construction
[0025] Below in conjunction with accompanying drawing, technical scheme of the present invention is described in further detail:
[0026] This invention may be embodied in many different forms and should not be construed as limited to the embodiments set forth herein. Rather, these embodiments are provided so that this disclosure will be thorough and complete, and will fully convey the scope of the invention to those skilled in the art. In the drawings, components are exaggerated for clarity.
[0027] Such as figure 1 As shown, the present invention discloses a space six-degree-of-freedom non-contact vibration isolation platform for aerospace, including a base, a working platform, and first to fourth electromagnetic vibration isolators arranged between the base and the working platform ;
[0028] The first to fourth electromagnetic isolators all include a first permanent magnet, a second permanent magnet, a permanent magnet mounting frame, an electromagnetic coil, and a coil m
PUM
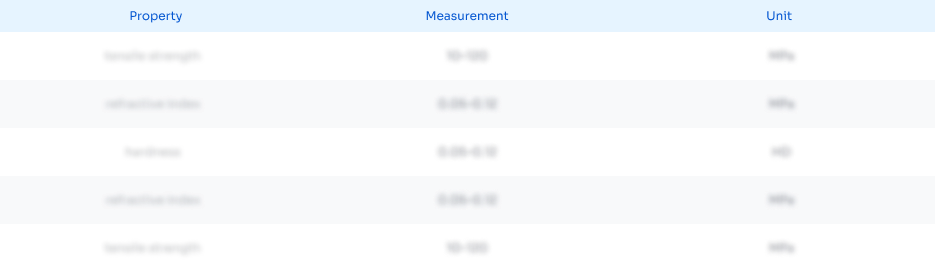
Abstract
Description
Claims
Application Information
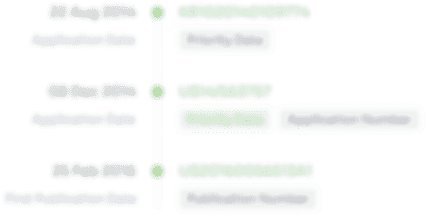
- R&D Engineer
- R&D Manager
- IP Professional
- Industry Leading Data Capabilities
- Powerful AI technology
- Patent DNA Extraction
Browse by: Latest US Patents, China's latest patents, Technical Efficacy Thesaurus, Application Domain, Technology Topic.
© 2024 PatSnap. All rights reserved.Legal|Privacy policy|Modern Slavery Act Transparency Statement|Sitemap