Gasification furnace with radiation heat exchange and gasification method
A radiation heat exchange and gasification furnace technology, applied in the field of coal chemical industry, can solve the problems of short operation period of the device, clogged slag and ash accumulation of waste pot, leakage of heat exchange tubes, etc., to reduce disturbance, increase slag passing diameter, reduce Effect of wall temperature
- Summary
- Abstract
- Description
- Claims
- Application Information
AI Technical Summary
Benefits of technology
Problems solved by technology
Method used
Image
Examples
Embodiment 1
[0051] This embodiment provides a gasifier with radiation heat exchange, the structure of which is as follows figure 1 As shown, it includes a shell 8 and a furnace body arranged in the shell 8. The furnace body includes a gasification chamber, a radiation heat exchange chamber 7 and a quench chamber which are arranged coaxially from top to bottom.
[0052] The gasification chamber includes a burner connection port at the top, a lower slag port 4 with swirling flow at the bottom, and a gasification reaction chamber 2 between the top and the bottom. The burner connection port and the gasification burner 1 connection, the gasification reaction chamber 2 is provided with a water-cooled wall 3; the casing 8 is provided with a gasification chamber water-cooled wall boiler water inlet N4 corresponding to the lower part of the gasification chamber, and the casing 8 corresponds to The upper part of the gasification chamber is provided with a steam and water outlet N3 of the water wall of the
Embodiment 2
[0063] This embodiment provides another gasifier with radiation heat exchange, the structure of which is as follows image 3 As shown, it includes a shell 8 and a furnace body arranged in the shell 8. The furnace body includes a gasification chamber, a radiation heat exchange chamber 7 and a quench chamber which are arranged coaxially from top to bottom.
[0064] The gasification chamber includes a burner connection port at the top, a lower slag port 4 with swirling flow at the bottom, and a gasification reaction chamber 2 between the top and the bottom. The burner connection port and the gasification burner 1 connection, the gasification reaction chamber 2 is provided with a water-cooled wall 3; the casing 8 is provided with a gasification chamber water-cooled wall boiler water inlet N4 corresponding to the lower part of the gasification chamber, and the casing 8 corresponds to The upper part of the gasification chamber is provided with a steam and water outlet N3 on the water wall
PUM
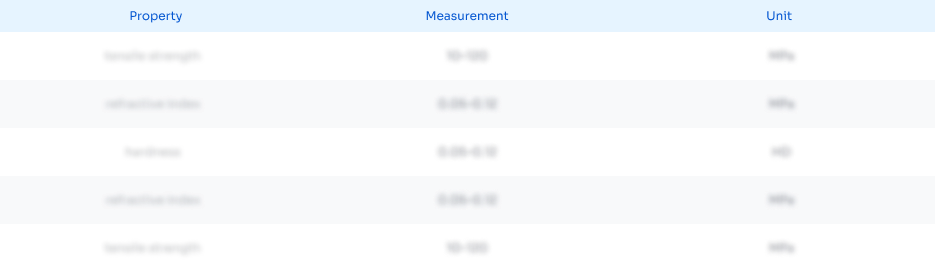
Abstract
Description
Claims
Application Information
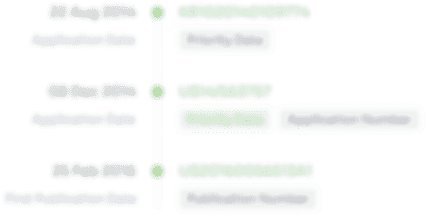
- R&D Engineer
- R&D Manager
- IP Professional
- Industry Leading Data Capabilities
- Powerful AI technology
- Patent DNA Extraction
Browse by: Latest US Patents, China's latest patents, Technical Efficacy Thesaurus, Application Domain, Technology Topic.
© 2024 PatSnap. All rights reserved.Legal|Privacy policy|Modern Slavery Act Transparency Statement|Sitemap