Manufacturing method of special-shaped transparent display screen
A technology of transparent display screen and manufacturing method, which is applied in manufacturing tools, glass manufacturing equipment, instruments, etc., can solve the problem of inability to manufacture special-shaped transparent display screens, and achieve the effect of ideal implementation effect and reasonable manufacturing process design.
- Summary
- Abstract
- Description
- Claims
- Application Information
AI Technical Summary
Benefits of technology
Problems solved by technology
Method used
Image
Examples
Embodiment Construction
[0034] A method for manufacturing a special-shaped transparent display screen, comprising the following steps:
[0035] The first step is cutting design and etching design of ITO glass and COVER glass;
[0036] When designing cutting, the principle of minimizing the remaining amount is the principle, taking into account the size of the glass, on the premise of providing a uniform voltage to the LED chip, considering the resistivity and optimizing the etching design at the same time, when designing the glass cutting method, try to consider The size of the remaining glass after cutting is easy to use again. Since 1mm of the edge needs to be consumed during cutting, the cutting design should be 1mm larger than the original design size;
[0037] When etching design, design the etching design according to the dimmers and their respective control methods;
[0038]When designing a parallelogram, in order to ensure the machining accuracy of the etching machine and the placement machine
PUM
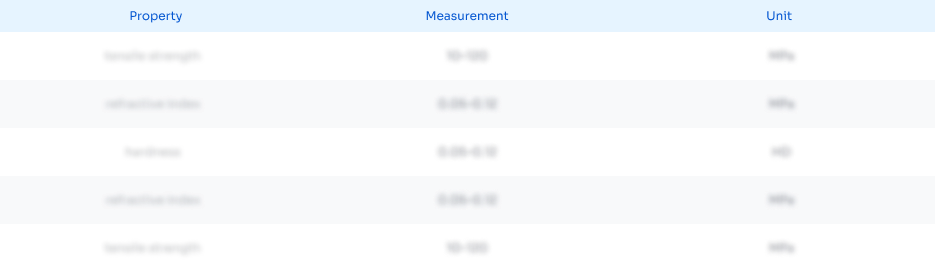
Abstract
Description
Claims
Application Information
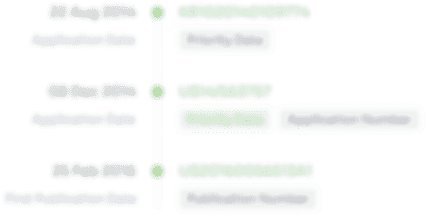
- R&D Engineer
- R&D Manager
- IP Professional
- Industry Leading Data Capabilities
- Powerful AI technology
- Patent DNA Extraction
Browse by: Latest US Patents, China's latest patents, Technical Efficacy Thesaurus, Application Domain, Technology Topic.
© 2024 PatSnap. All rights reserved.Legal|Privacy policy|Modern Slavery Act Transparency Statement|Sitemap