Truss structure rigidity and axial force structure identification method
A technology for truss structure and structure identification, applied in the directions of instrumentation, design optimization/simulation, electrical digital data processing, etc., can solve problems such as the impact of stiffness identification, and achieve the effect of less quantity demand and broad application prospects
- Summary
- Abstract
- Description
- Claims
- Application Information
AI Technical Summary
Benefits of technology
Problems solved by technology
Method used
Image
Examples
Embodiment Construction
[0017] The present invention will be further described below with reference to the accompanying drawings and examples.
[0018] Step 1: Build the model.
[0019] The truss structure consists of 10 nodes and 16 rods, including 4 upper chord rods, 4 lower chord rods, 4 web rods, each with a length of 500mm, and 4 diagonal web rods with a length of 707mm. 1.5mm thick hollow steel pipe. Create in ABAQUS such as image 3 For the 2D truss model shown, the elastic modulus of the section and Poisson's ratio are set to 210 GPa and 0.3, respectively, and the beam model is used for the members.
[0020] In order to consider the weakening of the stiffness of the member, another section property can be established. The geometric properties of this section are the same as those of the other sections of the original structure, and the stiffness is considered to be 0.5 times that of the other sections to characterize the damage of the member.
[0021] When dividing the mesh for the structure,
PUM
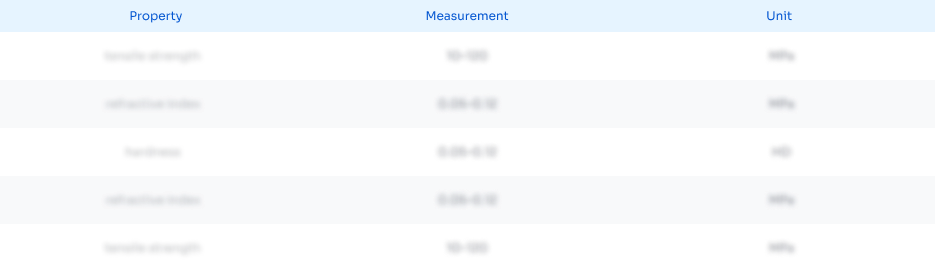
Abstract
Description
Claims
Application Information
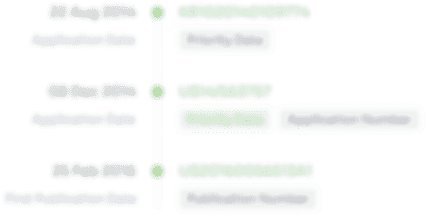
- R&D Engineer
- R&D Manager
- IP Professional
- Industry Leading Data Capabilities
- Powerful AI technology
- Patent DNA Extraction
Browse by: Latest US Patents, China's latest patents, Technical Efficacy Thesaurus, Application Domain, Technology Topic.
© 2024 PatSnap. All rights reserved.Legal|Privacy policy|Modern Slavery Act Transparency Statement|Sitemap