End-to-end high-precision industrial part shape modeling method
A modeling method and high-precision technology, which is applied in neural learning methods, biological neural network models, image data processing, etc., can solve the problem that the shape modeling of industrial parts cannot adapt to various data environments, and shorten debugging Time, large adaptability, simple effect of model debugging
- Summary
- Abstract
- Description
- Claims
- Application Information
AI Technical Summary
Benefits of technology
Problems solved by technology
Method used
Image
Examples
Embodiment 1
[0044] This embodiment provides an end-to-end high-precision shape modeling method for industrial parts. Such as figure 1 As shown, it mainly includes: S1: edge extraction, S2: building topological relationship between points, S3: point feature extraction, S4: point optimization. The four modules will be described separately below.
[0045] S1: Initial edge point extraction.
[0046] S1.1: Generate a depth map using the input point cloud.
[0047] S1.2: Mark the area of each part and its internal edge structure on the depth map as the ground truth for model training.
[0048] S1.3: Use Mask-RCNN on the depth map for target-level detection and semantic segmentation, and at the same time predict the distance between each pixel and its nearest edge point, referred to as the distance map.
[0049] S1.4: Obtain the area of each target detected by S1.3. In the distance map for this region, set pixel values less than 2 to 1, and to 0 otherwise. The result is the initial edge
PUM
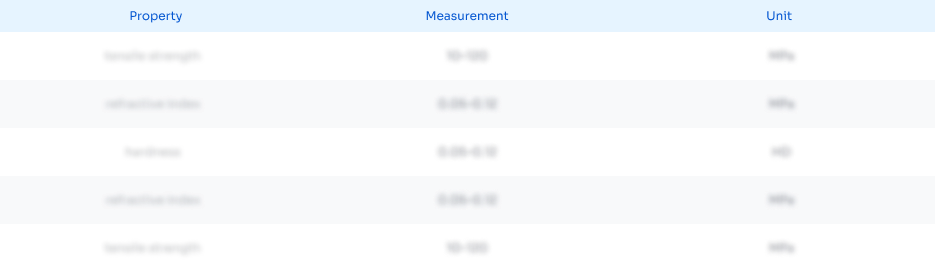
Abstract
Description
Claims
Application Information
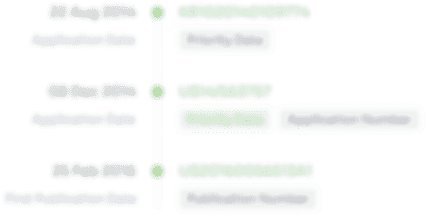
- R&D Engineer
- R&D Manager
- IP Professional
- Industry Leading Data Capabilities
- Powerful AI technology
- Patent DNA Extraction
Browse by: Latest US Patents, China's latest patents, Technical Efficacy Thesaurus, Application Domain, Technology Topic.
© 2024 PatSnap. All rights reserved.Legal|Privacy policy|Modern Slavery Act Transparency Statement|Sitemap