Calibration device and positioning method for regular geometry
A technology of calibration device and positioning method, applied in the direction of using mechanical device, measuring device, mechanical measuring device, etc., can solve the problems of large displacement of observation point geometry, inaccurate spatial position, etc., to achieve convenient operation, accurate calibration results, and simple structure. Effect
- Summary
- Abstract
- Description
- Claims
- Application Information
AI Technical Summary
Benefits of technology
Problems solved by technology
Method used
Image
Examples
Embodiment 1
[0046]SeeFigure 1-3 As shown, Embodiment 1 of the present application provides a calibration device for regular geometric bodies, which includes a flexible cover 1, a flexible measuring rule 2, a connecting mechanism 3, and two calibration mechanisms 5. The cover 1 is made of nylon. In order to ensure the bendability of the cover body 1; the measuring ruler 2 adopts 50# first-grade steel strip with a thickness of 0.10mm to ensure the bendability of the measuring ruler 2. The flexible measuring rule 2 is arranged on the cover 1 along the length direction of the cover 1; the connecting mechanism 3 is arranged on the cover 1 and is used to fix the cover 1 on the geometric body 4 to be measured; the calibration mechanism 5 is clamped in The measuring ruler 2 can be moved along the length direction of the measuring ruler 2.
[0047]The calibration device has a use state. When in use, the cover 1 is attached to the outer surface of the test geometry 4 along the circumferential direction of the
Embodiment 2
[0056]Embodiment 2 of the present application provides a positioning method suitable for regular geometric bodies, which includes the following steps:
[0057]S1: Provide the above-mentioned calibration device;
[0058]S2: Fit the cover 1 to the outer surface of the tested geometry 4 along the circumferential direction of the tested geometry 4, and fix the connecting mechanism 3 on the tested geometry 4 to fix the cover 1 and the tested geometry 4 ;
[0059]S3: Move the two calibration mechanisms 5 so that the difference between the scale values of the two calibration mechanisms 5 on the measuring ruler 2 is equal to half of the perimeter of the cross-section of the geometry 4 to be measured. The midpoint is the center of the cross-section of the geometry 4 to be measured, which realizes the calibration of the center of the cross-section of the geometry 4 to be measured;
[0060]S4: Measure the spatial positions of the two calibration mechanisms 5;
[0061]S5: According to the spatial position, the
PUM
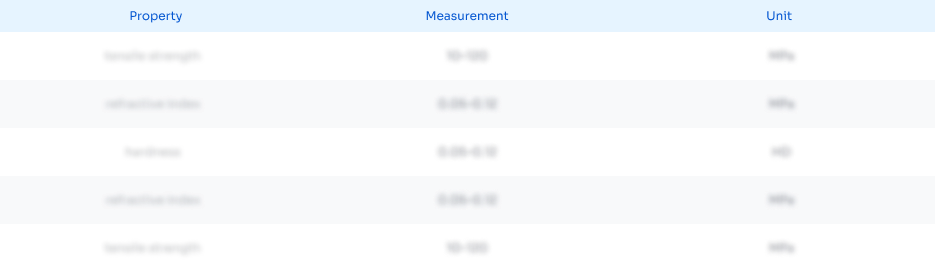
Abstract
Description
Claims
Application Information
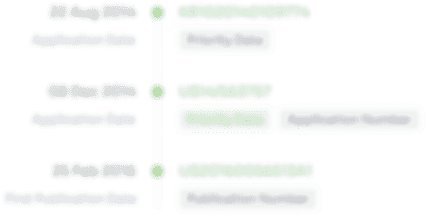
- R&D Engineer
- R&D Manager
- IP Professional
- Industry Leading Data Capabilities
- Powerful AI technology
- Patent DNA Extraction
Browse by: Latest US Patents, China's latest patents, Technical Efficacy Thesaurus, Application Domain, Technology Topic.
© 2024 PatSnap. All rights reserved.Legal|Privacy policy|Modern Slavery Act Transparency Statement|Sitemap