Method for controlling CaO inclusions in high-carbon steel wire rod
A control method and high carbon steel technology, applied in the field of iron and steel metallurgy to achieve the effect of improving yield
- Summary
- Abstract
- Description
- Claims
- Application Information
AI Technical Summary
Problems solved by technology
Method used
Image
Examples
Example Embodiment
[0022]Example 1
[0023]The ratio of CaO components in high CaO inclusions in high carbon steel wires is shown in the implementation of a high CaO clamp control method, as shown in Table 1. The specific embodiments are as follows:
[0024]1) converter smelting: The carbon content of the converter is 0.045%, the end point temperature is 1666 ° C, and the converter is not added to the addition of the carbonaceous agent. After the end of the steel, the steel is retaining steel 2.5T.
[0025]2) LF refining: According to the chemical composition of the LF to the station, the carbon chuck is adjusted to the target ingredient, the feed speed of the toner core wire is 4m / s, and the core wire is mixed. The type of SiO2-MnO is 1-5 mm. The alloy element of the other steel species is added to open the bottom of the steel pump, the bottom blowing strength is 4.5 L / (min T). After the steel hydraulic component reaches the target requirements, the bottom blow is closed, and 9kg / t high carbon steel
Example Embodiment
[0030]Example 2
[0031]The ratio of CaO components in high CaO inclusions in high carbon steel wires is shown in Table 2, through a high CaO clamp control method. The specific embodiments are as follows:
[0032]1) Converter smelting: The carbon content of the converter is 0.033%, the end point temperature is 1680 ° C, the converter does not add carbon, and the steel is retaining steel 4.5T.
[0033]2) LF refining: According to the chemical composition of the LF to the station, the carbon powder core wire is adjusted to the target component, the feed line of the carbon powder core is 6m / s, the core wire iron The inclusion type is a SiO2-MnO system, and the particle size of the toner is 1-5 mm. And the alloy element of the corresponding steel species is added, and the bottom blown bottom blow is opened, the bottom blowing strength is 5.7 L / (min T). After the steel hydraulic component reaches the target requirements, the bottom blow is closed, and the high carbon steel synthetic slag of
PUM
Property | Measurement | Unit |
---|---|---|
Granularity | aaaaa | aaaaa |
Abstract
Description
Claims
Application Information
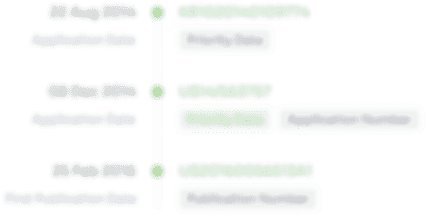
- R&D Engineer
- R&D Manager
- IP Professional
- Industry Leading Data Capabilities
- Powerful AI technology
- Patent DNA Extraction
Browse by: Latest US Patents, China's latest patents, Technical Efficacy Thesaurus, Application Domain, Technology Topic.
© 2024 PatSnap. All rights reserved.Legal|Privacy policy|Modern Slavery Act Transparency Statement|Sitemap