Helicopter blade covered edge forming method
A helicopter and hemming technology, which is applied in the direction of metal processing equipment, etc., can solve problems such as easy deformation, affecting performance, and inapplicability to hemming and forming of complex-shaped parts.
- Summary
- Abstract
- Description
- Claims
- Application Information
AI Technical Summary
Benefits of technology
Problems solved by technology
Method used
Image
Examples
Embodiment 1
[0050] It is estimated that the wall thickness of the hemming part obtained by forming processing is 0.5mm, and the length is 5m. image 3 A schematic diagram of the outline of the hemming parts is shown. A TC4 titanium alloy tube with an outer diameter of 190mm and a wall thickness of 0.6mm is used as the raw material. The TC4 titanium alloy tube is processed into a flat special-shaped tube by hot rolling, and the cross-sectional shape of the flat special-shaped tube is as follows Figure 4 shown. The flat special-shaped pipe is processed into a length of 5.5m by wire cutting method; the two end faces of the flat special-shaped pipe are welded with the same TC4 titanium alloy plate with the same cross-sectional shape as the flat special-shaped pipe respectively, and the TC4 titanium alloy plate is The thickness of the plate is 1mm, and a hole with a diameter of 8mm is processed in the middle of one of the TC4 titanium alloy plates, and a titanium alloy air expansion pipeline w
Embodiment 2
[0052] It is estimated that the wall thickness of the hemming part obtained by the forming process is 0.8mm, and the length is 10m. image 3 A schematic diagram of the outline of the hemming parts is shown. A TC4 titanium alloy tube with an outer diameter of 240mm and a wall thickness of 1.0mm is used as the raw material. The TC4 titanium alloy tube is processed into a flat special-shaped tube by hot rolling, and the cross-sectional shape of the flat special-shaped tube is as follows Figure 4 shown. The flat special-shaped pipe is processed by wire cutting to a length of 10.5m; the two ends of the flat special-shaped pipe are welded with argon arc welding, and TC4 titanium alloy plates with the same cross-sectional shape as the flat special-shaped pipe are respectively welded, and the thickness of the TC4 titanium alloy plate is 1mm. , and process a hole with a diameter of 8mm in the middle of one of the TC4 titanium alloy plates, and weld a titanium alloy air expansion pipeli
PUM
Property | Measurement | Unit |
---|---|---|
Wall thickness | aaaaa | aaaaa |
Abstract
Description
Claims
Application Information
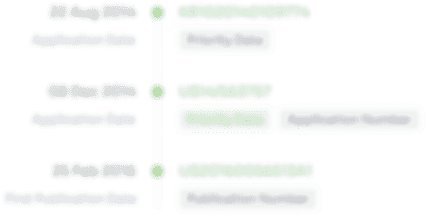
- R&D Engineer
- R&D Manager
- IP Professional
- Industry Leading Data Capabilities
- Powerful AI technology
- Patent DNA Extraction
Browse by: Latest US Patents, China's latest patents, Technical Efficacy Thesaurus, Application Domain, Technology Topic.
© 2024 PatSnap. All rights reserved.Legal|Privacy policy|Modern Slavery Act Transparency Statement|Sitemap