Collaborative turning track self-planning system and method for multi-body auxiliary transportation system
A technology that assists transportation and planning systems. It is used in signal transmission systems, transportation and packaging, and control/regulation systems. It can solve problems such as reducing impact force, difficult to meet production efficiency, and inability to correct driving trajectory.
- Summary
- Abstract
- Description
- Claims
- Application Information
AI Technical Summary
Problems solved by technology
Method used
Image
Examples
Embodiment 1
[0063] Such as figure 1 As shown, the multi-body auxiliary transportation system cooperative turning trajectory self-planning system of this embodiment is shown. The flatbed truck 1 for mining includes a front car 10, a rear car 11 and a connecting rod 12, and the front car 10 and the rear car 11 pass through the connecting rod 12. Connect; present embodiment is provided with image acquisition module 2 at the front end top of front car 10, is used for collecting mining platform vehicle 1 front environmental information and transmission; More specifically, image acquisition module 2 is composed of CCD binocular camera 20 and explosion-proof type The searchlight 21 is composed of the working environment of the mining flatbed truck 1 mostly in the mine roadway, and the light is insufficient. Therefore, the flameproof searchlight 21 is set to provide sufficient brightness for the image collected by the CCD binocular camera 20. The main purpose of the CCD binocular camera 20 is to shoo
Embodiment 2
[0070] The multi-body auxiliary transportation system cooperative turning trajectory self-planning method of this embodiment is based on the body-assisted transportation system cooperative turning trajectory self-planning system of embodiment 1, and the processing flow is as follows figure 2 As shown, the specific steps are as follows:
[0071] 1. Image acquisition:
[0072] When the mining flatbed truck 1 is moving, the image acquisition module 2 is started, the flameproof searchlight 21 is turned on, and the CCD binocular camera 20 captures the road information image ahead of the mining flatbed truck 1 in the driving direction, and transmits the image to the front vehicle control module through the USB port 30;
[0073] 2. Generate target trajectory:
[0074] a1, extracting edge features, the control module 3 establishes an image coordinate system according to the received image information, the horizontal axis is the u axis, the vertical axis is the v axis, defines the curv
PUM
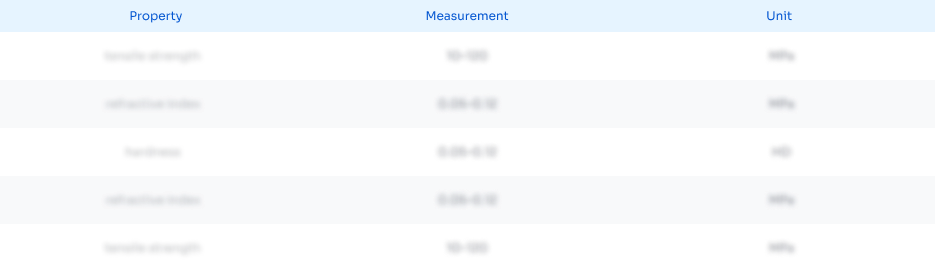
Abstract
Description
Claims
Application Information
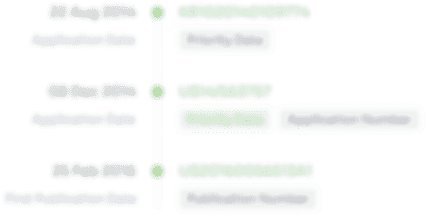
- R&D Engineer
- R&D Manager
- IP Professional
- Industry Leading Data Capabilities
- Powerful AI technology
- Patent DNA Extraction
Browse by: Latest US Patents, China's latest patents, Technical Efficacy Thesaurus, Application Domain, Technology Topic.
© 2024 PatSnap. All rights reserved.Legal|Privacy policy|Modern Slavery Act Transparency Statement|Sitemap