Single-polarization low-optical-noise space micromirror coupling system and digital signal processing system
A space micromirror and coupling system technology, applied in the coupling of optical waveguides, optics, optical components, etc., can solve the problems of optical noise interference and large loss, reduce coupling loss, suppress polarization noise, and suppress optical Kerr effect of noise
- Summary
- Abstract
- Description
- Claims
- Application Information
AI Technical Summary
Benefits of technology
Problems solved by technology
Method used
Image
Examples
Embodiment 1
[0025] figure 1 It is a schematic structural diagram of a single polarization low optical noise spatial micromirror coupling system provided by an embodiment of the present invention. The low optical noise spatial coupling system includes a first polarization-maintaining fiber interface 1, a first aspheric lens 2, a first beam splitter Mirror 3, second aspheric lens 4, first photodetector 5, third aspheric lens 6, plane beam splitter, fourth aspheric lens 9, second beam splitter 10, fifth aspheric lens 11, the first Six aspheric lenses 12 , a second photodetector 13 , a second polarization-maintaining fiber interface 14 , a first hollow-core photonic crystal fiber interface 15 , a second hollow-core photonic crystal fiber interface 16 , and a hollow-core photonic crystal fiber resonant cavity 17 . Among them, the diameter of the six groups of aspheric lenses is 4.7mm, the focal length is 6.2mm, the splitting ratio of the two groups of beam mirrors is 0.9, and the reflection coeff
Embodiment 2
[0031] This embodiment provides a digital signal processing system of a hollow-core photonic crystal fiber gyroscope, the method is based on the low optical noise spatial coupling system described in Embodiment 1, such as Figure 4 As shown, including the tunable laser Tunable Laser, the light emitted by the tunable laser Tunable Laser passes through the phase modulator PM0 and then is split by the signal beam splitter C1 to obtain the second clockwise CW light and the second counterclockwise CCW The second clockwise CW light enters the phase modulator PM2, the intensity modulator IM2, the optical fiber circulator C3, and the polarization-maintaining optical fiber interface PMF1 (corresponding to figure 1 In the first polarization-maintaining fiber interface 1), then through figure 1 The shown spatial coupling system enters the hollow-core photonic crystal resonator 17, and the multi-beam interference results from the polarization-maintaining fiber interface PMF2 (corresponding t
PUM
Property | Measurement | Unit |
---|---|---|
Thickness | aaaaa | aaaaa |
Abstract
Description
Claims
Application Information
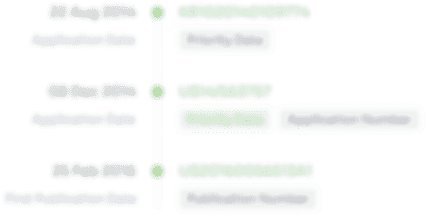
- R&D Engineer
- R&D Manager
- IP Professional
- Industry Leading Data Capabilities
- Powerful AI technology
- Patent DNA Extraction
Browse by: Latest US Patents, China's latest patents, Technical Efficacy Thesaurus, Application Domain, Technology Topic.
© 2024 PatSnap. All rights reserved.Legal|Privacy policy|Modern Slavery Act Transparency Statement|Sitemap