Welding equipment for air inlet temperature and pressure sensor machining
A technology of pressure sensor and intake air temperature, which is applied in welding equipment, auxiliary welding equipment, metal processing equipment, etc., can solve the problems of affecting the normal operation of the equipment, poor environmental protection, and affecting the working environment, so as to meet the requirements of high-precision welding and improve Welding stability, the effect of improving product quality
- Summary
- Abstract
- Description
- Claims
- Application Information
AI Technical Summary
Problems solved by technology
Method used
Image
Examples
Example Embodiment
[0030] The technical solution of the present patent will be described in further detail below in conjunction with specific embodiments.
[0031] like Figure 1-6As shown, the present invention provides a technical solution: a welding equipment for processing an intake air temperature and pressure sensor, comprising a base plate 1, the upper surface of the base plate 1 is fixedly connected with the lower surface of the equipment box 2, and the upper surface of the equipment box 2 is welded to The lower surface of the table 3 is fixedly connected, the upper surface of the welding table 3 is provided with a control panel 4, the left side of the front of the control panel 4 is provided with a warning light 5, and the upper surface of the inner wall of the welding table 3 is provided with three welding mechanisms 8, the welding mechanism 8 A support assembly 10 is arranged below the welding table 3, the front of the inner wall of the welding table 3 is fixedly connected to one end of
PUM
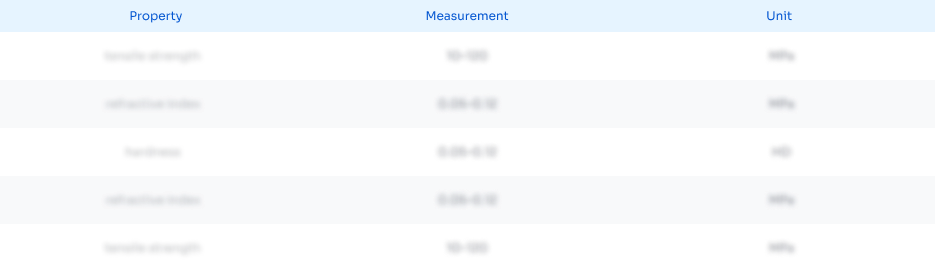
Abstract
Description
Claims
Application Information
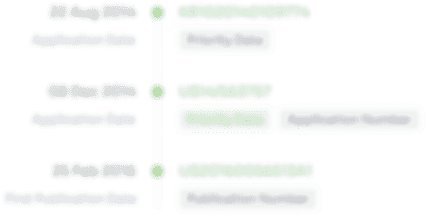
- R&D Engineer
- R&D Manager
- IP Professional
- Industry Leading Data Capabilities
- Powerful AI technology
- Patent DNA Extraction
Browse by: Latest US Patents, China's latest patents, Technical Efficacy Thesaurus, Application Domain, Technology Topic.
© 2024 PatSnap. All rights reserved.Legal|Privacy policy|Modern Slavery Act Transparency Statement|Sitemap