Chemical purification method for preparing ultralow ash content coal from clean coal
A chemical purification and ultra-low ash technology, applied in chemical instruments and methods, inorganic chemistry, silicon oxide, etc., can solve problems such as ineffective recovery of valuable substances, high acid and alkali consumption, and difficulty in waste liquid treatment
- Summary
- Abstract
- Description
- Claims
- Application Information
AI Technical Summary
Benefits of technology
Problems solved by technology
Method used
Image
Examples
Embodiment 1
[0041] This example discloses a chemical purification method for producing ultra-low ash coal from clean coal, see figure 1 , is a process flow diagram of the present invention. The clean coal: 5% ash.
[0042] Include the following steps:
[0043] S1. Oxygen barrier activated roasting: In an oxygen-free environment, the temperature is 950 ° C, and the coal with 5% ash content is roasted for 40 minutes. The aluminosilicate minerals in the ash are activated to form amorphous SiO 2 and a'-Al 2 o 3 ;Carbon burning rate of 1.5% in the roasting process;
[0044] S2. Separation of silicon by alkali dissolution at low temperature: adding Na to the activated roasting product obtained in S1 2 Ok concentration is 100g / L caustic alkali solution, temperature 100 ℃, reaction 3h, filter to obtain aluminum-containing coal and silicon-containing filtrate;
[0045] S3. High-temperature alkali-dissolution separation of aluminum: the aluminum-containing coal obtained in S2 is added to the s
Embodiment 2
[0048] This example discloses a chemical purification method for producing ultra-low ash coal from clean coal, see figure 1 , is a process flow diagram of the present invention. The clean coal: 3% ash.
[0049] Include the following steps:
[0050] S1. Oxygen barrier activated roasting: In an oxygen-free environment, the temperature is 1000 ° C, and the coal with ash content of 3% is roasted for 30 minutes. The aluminosilicate minerals in the ash are activated to form amorphous SiO 2 and a'-Al 2 o 3 ;Carbon burning loss aluminum 1.8% in the roasting process;
[0051] S2. Separation of silicon by alkali dissolution at low temperature: adding Na to the activated roasting product obtained in S1 2 Ok concentration is 130g / L caustic alkali solution, temperature 95 ℃, react for 2h, filter to obtain aluminum-containing coal and silicon-containing filtrate;
[0052] S3. High-temperature alkali-dissolution separation of aluminum: the aluminum-containing coal obtained in S2 is adde
Embodiment 3
[0055] This example discloses a chemical purification method for producing ultra-low ash coal from clean coal, see figure 1 , is a process flow diagram of the present invention. The clean coal: ash content 3.5%.
[0056] Include the following steps:
[0057] S1. Oxygen barrier activated roasting: In an oxygen-free environment, the temperature is 1050 ° C, and the coal with ash content of 3.5% is roasted for 20 minutes. The aluminosilicate minerals in the ash are activated to form amorphous SiO 2 and a'-Al 2 o 3 2.2% of aluminum is lost by carbon burning in the roasting process;
[0058] S2. Separation of silicon by alkali dissolution at low temperature: adding Na to the activated roasting product obtained in S1 2 Ok concentration is 150g / L caustic alkali solution, temperature 110 ℃, react for 1h, filter to obtain aluminum-containing coal and silicon-containing filtrate;
[0059] S3. High-temperature alkali-dissolution separation of aluminum: the aluminum-containing coal o
PUM
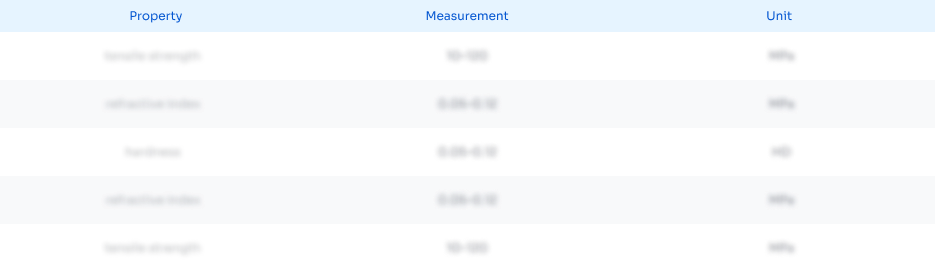
Abstract
Description
Claims
Application Information
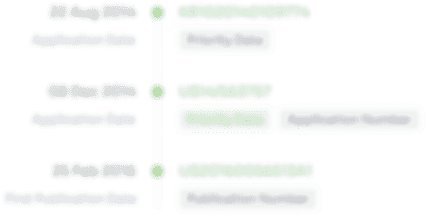
- R&D Engineer
- R&D Manager
- IP Professional
- Industry Leading Data Capabilities
- Powerful AI technology
- Patent DNA Extraction
Browse by: Latest US Patents, China's latest patents, Technical Efficacy Thesaurus, Application Domain, Technology Topic.
© 2024 PatSnap. All rights reserved.Legal|Privacy policy|Modern Slavery Act Transparency Statement|Sitemap