Apparatus and buffing element for reconditioning digital recording discs
a technology buffing elements, applied in the field of reconditioning the protective surface of digital recording discs, can solve the problems of many used discs not being resold, affecting playback quality and visual appearance, and interfering with the laser beam before it reaches the data layer, etc., to achieve the effect of restoring both playback quality and visual appearance, and effectively reconditioning the protective surface of the dis
- Summary
- Abstract
- Description
- Claims
- Application Information
AI Technical Summary
Benefits of technology
Problems solved by technology
Method used
Image
Examples
Embodiment Construction
[0025] FIG. 1 shows a diagram of an optically-read digital recording disc 20. optically-read digital recording disc 20 generally includes a center section, or clamping area 22, located about a center hole 24 of disc 20. Surrounding clamping area 22 is a narrow text band 26 typically used to identify the manufacturer. Clamping area 22 and text band 26 to not contain encoded data. A data layer 28 lies outside of text band 26. Data layer 28 is arranged in spiral tracks and is covered by a protective surface 30. Disc 20 is shown with a portion of protective surface 30 removed to show the underlying spiral arranged data layer 28. An abrasion pattern 32 created in accordance with a disc reconditioning apparatus is shown on protective surface 30 and will be described in detail below.
[0026] When disc 20 is a music compact disc (CD), the first band of data layer 28 closest to text band 26, called the "lead-in", contains the table of contents for the CD. The lead-in tells the CD playback equipme
PUM
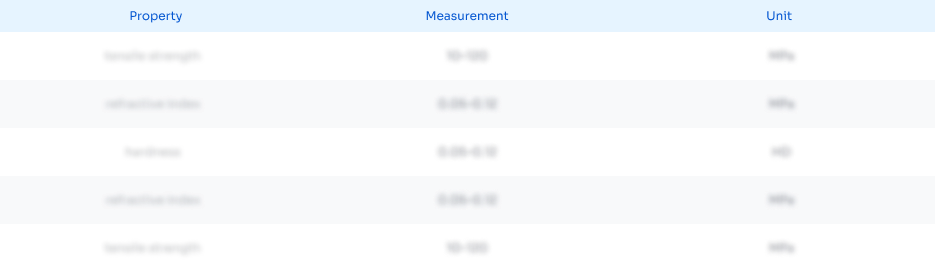
Abstract
Description
Claims
Application Information
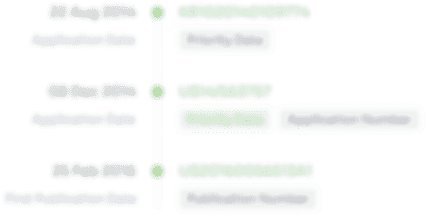
- R&D Engineer
- R&D Manager
- IP Professional
- Industry Leading Data Capabilities
- Powerful AI technology
- Patent DNA Extraction
Browse by: Latest US Patents, China's latest patents, Technical Efficacy Thesaurus, Application Domain, Technology Topic.
© 2024 PatSnap. All rights reserved.Legal|Privacy policy|Modern Slavery Act Transparency Statement|Sitemap