Pressure-sensitive adhesive sheet
- Summary
- Abstract
- Description
- Claims
- Application Information
AI Technical Summary
Benefits of technology
Problems solved by technology
Method used
Examples
Example
EXAMPLE 1
[0091] Using a reaction vessel (separable flask) fitted with a condenser tube, a nitrogen-inlet tube, a thermometer, and a stirrer, 0.1 part of 2,2′-azobis[N-(2-carboxyethyl)-2-methylpropionamidine] hydrate (trade name “VA-057” manufactured by Wako Pure Chemical Industries, Ltd.) as a polymerization initiator and 40 parts of ion exchange water were charged thereto and the whole was stirred for 1 hour and heated to 60° C. with introducing nitrogen gas. Thereafter, an emulsified product obtained by adding 68 parts of butyl acrylate, 29 parts of 2-ethylhexyl acrylate, 2.9 parts of acrylic acid, and 8 parts of an aqueous solution containing sodium polyoxyethylene alkylphenyl ether sulfate in an amount of 26% by weight (emulsifier) to 24.3 parts of water and emulsifying them were added dropwise into the above reaction vessel under stirring at 60° C. over a period of 4 hours and further aging was conducted for 3 hours. After polymerization, 10% aqueous ammonia was added to adjust t
Example
EXAMPLE 2
[0093] A pressure-sensitive adhesive sheet (double-sided pressure-sensitive adhesive sheet) was prepared in the same manner as in Example 1 except that a trade name “Super Ester E-720” (manufactured by Arakawa Chemical Industries, Ltd.; a stabilized rosin ester; ratio of components having a molecular weight of 300 or less: 3.92% by weight) as a tackifier was used in an amount of 30 parts in terms of solid matter relative to 100 parts of the acrylic polymer in the water-dispersion type acrylic polymer composition.
Example
EXAMPLE 3
[0094] A pressure-sensitive adhesive sheet (double-sided pressure-sensitive adhesive sheet) was prepared in the same manner as in Example 1 except that a trade name “04-039” (manufactured by Arakawa Chemical Industries, Ltd.; a polymerized rosin ester; ratio of components having a molecular weight of 300 or less: 4.06% by weight) as a tackifier was used in an amount of 30 parts in terms of solid matter relative to 100 parts of the acrylic polymer in the water-dispersion type acrylic polymer composition.
PUM
Property | Measurement | Unit |
---|---|---|
Percent by mass | aaaaa | aaaaa |
Mass | aaaaa | aaaaa |
Fraction | aaaaa | aaaaa |
Abstract
Description
Claims
Application Information
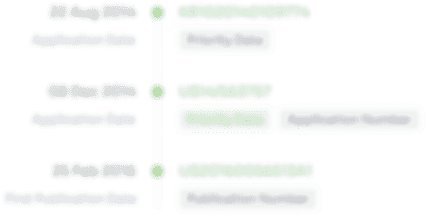
- R&D Engineer
- R&D Manager
- IP Professional
- Industry Leading Data Capabilities
- Powerful AI technology
- Patent DNA Extraction
Browse by: Latest US Patents, China's latest patents, Technical Efficacy Thesaurus, Application Domain, Technology Topic.
© 2024 PatSnap. All rights reserved.Legal|Privacy policy|Modern Slavery Act Transparency Statement|Sitemap