Method of fabricating microphone device and thermal oxide layer and low-stress structural layer thereof
a technology of thermal oxide layer and microphone device, which is applied in the direction of electrostatic transducer microphone, microelectromechanical system, electrical transducer, etc., can solve the problems of mediocre physical characteristics of the deposited oxide layer b>12/b>, and the need for extremely long time to thermally form the oxide layer of several micrometers thick,
- Summary
- Abstract
- Description
- Claims
- Application Information
AI Technical Summary
Benefits of technology
Problems solved by technology
Method used
Image
Examples
Embodiment Construction
[0016] Referring to FIG. 7 to FIG. 15, FIG. 7 to FIG. 15 are schematic diagrams illustrating a method of fabricating a microphone device in accordance with a preferred embodiment of the present invention. It is appreciated that FIG. 7 to FIG. 15 only illustrate one microphone device, and the fabrication of microphone device may be divided into three stages: the first stage is to form a thermal oxide layer (illustrated in FIG. 7 to FIG. 9); the second stage is to form a structural layer (illustrated in FIG. 10 to FIG. 13); and the third stage is to form a back chamber (illustrated in FIG. 14 and FIG. 15).
[0017] As shown in FIG. 7, a substrate 50 e.g. a silicon wafer or an SOI wafer is provided. Subsequently, a plurality of trenches 52 are formed in the front surface of the substrate 50 by deep etching techniques such as inductively coupled plasma reactive ion etching (ICPRIE), deep X ray lithography, or electron cyclotron resonance (ECR) plasma etching. In this embodiment, the line wid
PUM
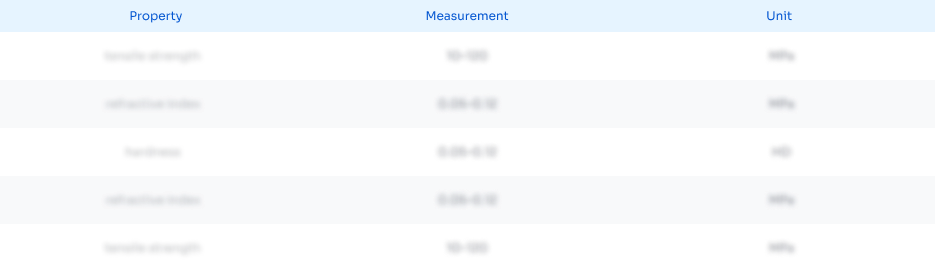
Abstract
Description
Claims
Application Information
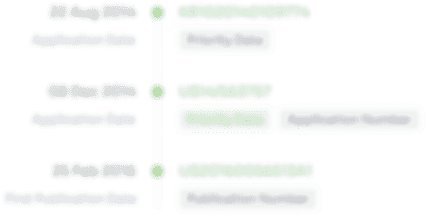
- R&D Engineer
- R&D Manager
- IP Professional
- Industry Leading Data Capabilities
- Powerful AI technology
- Patent DNA Extraction
Browse by: Latest US Patents, China's latest patents, Technical Efficacy Thesaurus, Application Domain, Technology Topic.
© 2024 PatSnap. All rights reserved.Legal|Privacy policy|Modern Slavery Act Transparency Statement|Sitemap