Method and apparatus for heat treating a fuel assembly channel made of a zirconium alloy
a technology of fuel assembly channel and zirconium alloy, which is applied in the direction of lighting and heating apparatus, furnace types, reactor fuel elements, etc., can solve the problems of different material parameters of corner regions and wall regions, and achieve the effects of less power, increased inductive coupling, and greater variability
- Summary
- Abstract
- Description
- Claims
- Application Information
AI Technical Summary
Benefits of technology
Problems solved by technology
Method used
Image
Examples
Embodiment Construction
[0025] Referring now to the figures of the drawing in detail and first, particularly, to FIGS. 1-4 thereof, there is shown an apparatus for heat treating a fuel assembly channel or box 1. The apparatus contains a housing 2, which is carried vertically, or in a longitudinal direction 3 of the channel, on a non-illustrated frame, a heating zone 4 having a first heating device 4a and a second heating device 4b and a nozzle configuration 6 forming a first cooling zone 7. The housing 2 contains a cylinder made of glass, that is to say of a material permeable to electromagnetic fields. The housing 2 furthermore contains an upper flange 9 and a lower flange 10, both flanges 9, 10 being approximately in the form of a circular disk and being linked via bars 12, which are disposed coaxially outside a cylinder 8. The flanges 9, 10 have in each case a central opening 13 and 14 respectively. The shape of the openings 13, 14 complements the contour of the fuel assembly channel 1, which passes throug
PUM
Property | Measurement | Unit |
---|---|---|
Time | aaaaa | aaaaa |
Temperature | aaaaa | aaaaa |
Electrical conductivity | aaaaa | aaaaa |
Abstract
Description
Claims
Application Information
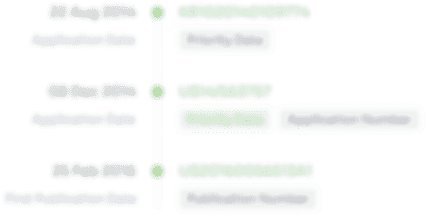
- R&D Engineer
- R&D Manager
- IP Professional
- Industry Leading Data Capabilities
- Powerful AI technology
- Patent DNA Extraction
Browse by: Latest US Patents, China's latest patents, Technical Efficacy Thesaurus, Application Domain, Technology Topic.
© 2024 PatSnap. All rights reserved.Legal|Privacy policy|Modern Slavery Act Transparency Statement|Sitemap