Baffled sun sensor antenna alignment monitors
a technology of sun sensor and antenna alignment, which is applied in the direction of optical radiation measurement, instruments for comonautical navigation, instruments, etc., can solve the problems of no devices that remotely monitor antenna alignment, hands-on alignment is a significant cost to owners of directional and omni-directional antennas, and no all-inclusive method to double-check tower crew measurements
- Summary
- Abstract
- Description
- Claims
- Application Information
AI Technical Summary
Benefits of technology
Problems solved by technology
Method used
Examples
third embodiment
[0040]sensor 1B of the invention is shown in FIG. 11 and can be made by using the basic parts described above and mounting them to the output shaft 33 of a secondary motor 34 through another mounting plate 35 which replaces the motor mount 32 of previous embodiment. This secondary motor 34 is either a stepper motor, which moves a precise step distance on command, or a servo type with a rotary position feedback device. This is important because the exact rotational position of the motor and thereby the baffle 9 with the phototransistor sensor 8 with respect to both axes of motion must be known at all times. A start position for this measurement is given by a second homing switch 30′, which can be one of several types commonly used for this purpose. This homing switch 30′ senses the position of the printed circuit board 27 and the mounting plate 35 so that a reference traceable back to the mounting of the sensor base 31 to the antenna (not shown) may be established. This allows the se...
fourth embodiment
[0042]the invention is disclosed in FIGS. 12 through 15. This is a fixed, multi-element mask sensor 1C with the baffling accomplished by a stack of flat opaque plates 40 with slots 41 having angled side walls 50 molded into them that define narrow slits 52 that function the same as the slits described with respect to the sensor 1. The phototransistor sensors 42 are arranged in a circle facing up on a printed circuit board 43, see FIG. 15, so as to be below the stack of plates. The phototransistor sensors 42 have a view completely blocked by the flat opaque plates 40 above, except for where a set of the radial slots 41 line up directly above each phototransistor sensor 42. This slot configuration can be attained by the use of a set of three very thin opaque plates spaced apart vertically with very narrow aligned slits cut in them, or preferably by a set of six plates, as shown in the drawings, with alternating wider slots with at least one angled side 50 which overlap slightly, creat...
PUM
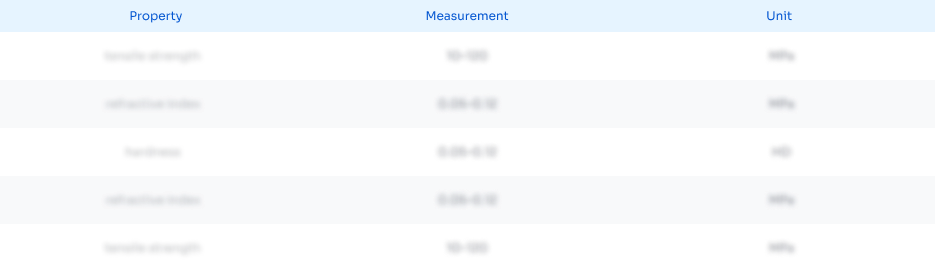
Abstract
Description
Claims
Application Information
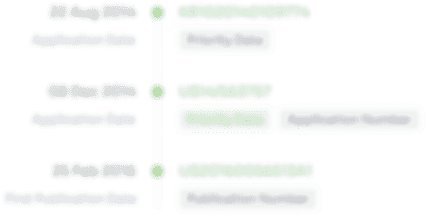
- R&D Engineer
- R&D Manager
- IP Professional
- Industry Leading Data Capabilities
- Powerful AI technology
- Patent DNA Extraction
Browse by: Latest US Patents, China's latest patents, Technical Efficacy Thesaurus, Application Domain, Technology Topic.
© 2024 PatSnap. All rights reserved.Legal|Privacy policy|Modern Slavery Act Transparency Statement|Sitemap