Low Pressure Transducer Using Beam and Diaphragm
a low-pressure transducer and beam technology, applied in the field of fluid pressure sensors, can solve the problems of high strain level, affecting both sensitivity and accuracy, and metal diaphragms showing undesirable interactions
- Summary
- Abstract
- Description
- Claims
- Application Information
AI Technical Summary
Benefits of technology
Problems solved by technology
Method used
Image
Examples
Embodiment Construction
[0016]It is to be understood that the figures and descriptions of the present invention have been simplified to illustrate elements that are relevant for a clear understanding of the present invention, while eliminating, for purposes of clarity, many other elements found in typical pressure sensing methods and systems. However, because such elements are well known in the art, and because they do not facilitate a better understanding of the present invention, a discussion of such elements is not provided herein. The disclosure herein is directed to all such variations and modifications known to those skilled in the art.
[0017]The present invention relates to a low pressure metal transducer that utilizes silicon strain gages glass bonded to a raised metal surface also referred to as a cross beam, which is formed from metal stock integral to a metal diaphragm formed from a cylindrical section. The ratio of the area of diaphragm top surface embodying the metal beam to the total area of the
PUM
Property | Measurement | Unit |
---|---|---|
Thickness | aaaaa | aaaaa |
Thickness | aaaaa | aaaaa |
Thickness | aaaaa | aaaaa |
Abstract
Description
Claims
Application Information
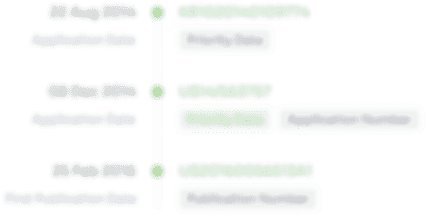
- R&D Engineer
- R&D Manager
- IP Professional
- Industry Leading Data Capabilities
- Powerful AI technology
- Patent DNA Extraction
Browse by: Latest US Patents, China's latest patents, Technical Efficacy Thesaurus, Application Domain, Technology Topic.
© 2024 PatSnap. All rights reserved.Legal|Privacy policy|Modern Slavery Act Transparency Statement|Sitemap