Coating system for clearance control in rotating machinery
a technology for rotating machinery and sealing systems, which is applied in the direction of machines/engines, liquid fuel engines, superimposed coating processes, etc., can solve the problems of affecting the sealing effect, so as to reduce the loss of blade tips, improve sealing effect, and reduce the effect of sealing temperatur
- Summary
- Abstract
- Description
- Claims
- Application Information
AI Technical Summary
Benefits of technology
Problems solved by technology
Method used
Examples
Embodiment Construction
[0011]As indicated above, this invention relates in part to a gas turbine engine seal system comprising a rotating member having an abrasive tip surface disposed in rub relationship to a stationary abradable seal surface, wherein said abrasive tip surface comprises an abrasive coating deposited onto at least a portion of the tip surface, wherein said abrasive coating comprises a metallic alloy matrix having ceramic abrasive particles at least partially embedded in said matrix and at least some of the ceramic abrasive particles projecting from said matrix, wherein said ceramic abrasive particles are selected from alumina polycrystal, alumina single crystal (sapphire), chromia-doped alumina single crystal (ruby), yttria-alumina garnet (YAG), titania-doped alumina polycrystal or single crystal (emerald), SiAlON, SiC, Si3N4 or diamond; wherein said abradable seal surface comprises an abradable ceramic coating deposited onto at least a portion of the seal surface; and wherein said gas turbi
PUM
Property | Measurement | Unit |
---|---|---|
Fraction | aaaaa | aaaaa |
Thickness | aaaaa | aaaaa |
Thickness | aaaaa | aaaaa |
Abstract
Description
Claims
Application Information
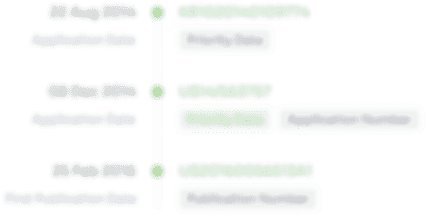
- R&D Engineer
- R&D Manager
- IP Professional
- Industry Leading Data Capabilities
- Powerful AI technology
- Patent DNA Extraction
Browse by: Latest US Patents, China's latest patents, Technical Efficacy Thesaurus, Application Domain, Technology Topic.
© 2024 PatSnap. All rights reserved.Legal|Privacy policy|Modern Slavery Act Transparency Statement|Sitemap