Surface charge reduction technique for capacitive sensors
a capacitive sensor and surface charge technology, applied in the direction of resistance/reactance/impedence, instruments, measurement devices, etc., can solve the problems of signal transfer to the input of the amplifier, surface charge build-up, and disturbance of the system operation
- Summary
- Abstract
- Description
- Claims
- Application Information
AI Technical Summary
Benefits of technology
Problems solved by technology
Method used
Examples
Embodiment Construction
[0036]FIG. 6 represents a top-level view of three variations of a differential circuit, for example the differential circuit of FIG. 4. FIG. 6(a) represents the differential circuit as shown in FIG. 4, which as explained above has a non-zero average voltage across the electrodes in the transducer 402. FIG. 6(b) represents the differential circuit as shown in FIG. 4 with the bridge capacitor inputs inverted. This only reverses the polarity of the voltage waveforms on the bridge capacitors, which does nothing to reduce the non-zero average voltage across the electrodes. FIG. 6(c) represents the differential circuit as shown in FIG. 4 with the inputs to the bridge capacitors swapped. This only moves the voltage waveform from core CA to core CB and moves the voltage waveform from core CB to CA, which also does nothing to reduce the non-zero average voltage across the electrodes. In essence, all three circuits in FIG. 6 are the same. It would be desirable to design a circuit that has a s...
PUM
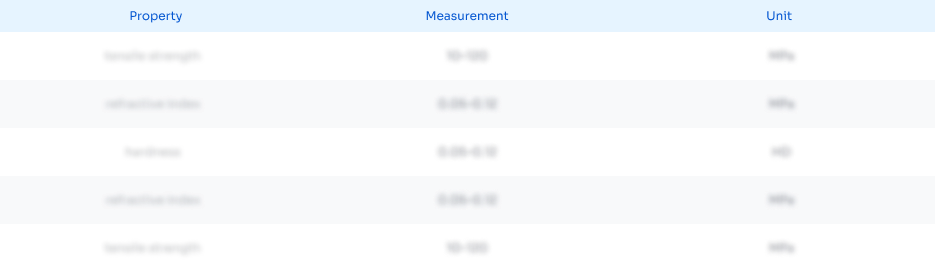
Abstract
Description
Claims
Application Information
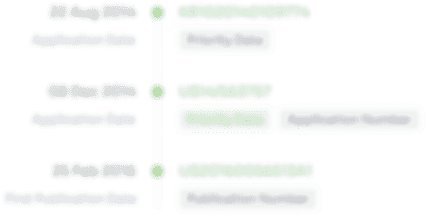
- R&D Engineer
- R&D Manager
- IP Professional
- Industry Leading Data Capabilities
- Powerful AI technology
- Patent DNA Extraction
Browse by: Latest US Patents, China's latest patents, Technical Efficacy Thesaurus, Application Domain, Technology Topic.
© 2024 PatSnap. All rights reserved.Legal|Privacy policy|Modern Slavery Act Transparency Statement|Sitemap