Position measuring device
- Summary
- Abstract
- Description
- Claims
- Application Information
AI Technical Summary
Benefits of technology
Problems solved by technology
Method used
Examples
Example
First Embodiment
[0028]FIG. 1 is a configuration diagram illustrating a position measuring device according to a first embodiment.
[0029]As illustrated in FIG. 1, a position measuring device 1 according to the present embodiment includes a light emitter 10, a hologram 20, a light receiver 30, and a measurement unit 40. The position measuring device 1 irradiates a workpiece W as an object with a laser light LS1 and receives light reflected and scattered by a surface of the workpiece W (hereinafter referred to as “detection light LS2”). Thus, the position measuring device 1 measures a position on the surface of the workpiece W at which the laser light LS1 is incident in a non-contact manner.
[0030]The light emitter 10 has a laser light source configured to emit the laser light LS1. The light emitter 10 emits the laser light LS1 toward the workpiece W during measurement.
[0031]The hologram 20 is positioned at a position where the hologram 20 does not intercept the optical axis c of the laser
Example
Second Embodiment
[0059]A position measuring device according to a second embodiment will now be described.
[0060]FIGS. 6A and 6B are configuration diagrams illustrating a position measuring device according to the second embodiment.
[0061]As illustrated in FIGS. 6A and 6B, a position measuring device 1B according to the present embodiment is different from the position measuring device 1 according to the first embodiment in the configuration of a hologram 21. The position measuring device 1B also includes a drive mechanism 60 for the hologram 21. Other configurations are the same as the position measuring device 1.
[0062]The hologram 21 used in the position measuring device 1B has a first area 211 and a second area 212. The first area 211 is an area that generates a first inclined surface inclined at a first angle relative to the optical axis c of the laser light LS1 as a reconstructed image. The second area 212 is an area that generates a second inclined surface inclined at a second ang
Example
Third Embodiment
[0068]A position measuring device according to a third embodiment will now be described.
[0069]FIG. 7 is a configuration diagram illustrating a position measuring device according to the third embodiment.
[0070]As illustrated in FIG. 7, a position measuring device 1C includes a lens 70 between the hologram 20 and the light receiver 30. Other configurations are the same as the position measuring device 1 according to the first embodiment.
[0071]The lens 70 has a characteristic of expanding the reconstructed image generated by the hologram 20. Such a lens 70 allows the light receiver 30 to capture a change in the image position of the hologram 20 associated with a change in the position of the workpiece W under magnification when the position of the workpiece W is measured. This makes it possible to detect a small height change in the position of the workpiece W with high accuracy.
[0072]As described above, the position measuring devices 1, 1B, and 1C according to the embodi
PUM
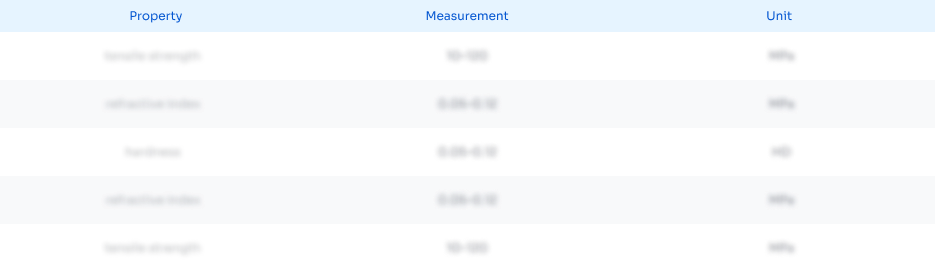
Abstract
Description
Claims
Application Information
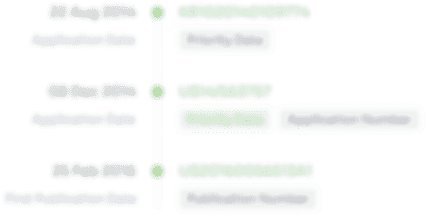
- R&D Engineer
- R&D Manager
- IP Professional
- Industry Leading Data Capabilities
- Powerful AI technology
- Patent DNA Extraction
Browse by: Latest US Patents, China's latest patents, Technical Efficacy Thesaurus, Application Domain, Technology Topic.
© 2024 PatSnap. All rights reserved.Legal|Privacy policy|Modern Slavery Act Transparency Statement|Sitemap