Flexographic printing plate
a printing plate and flexographic technology, applied in the field of flexographic printing plates, can solve the problems of ink density drop and ink transferability, and achieve the effect of good printing quality and excellent ink transferability
- Summary
- Abstract
- Description
- Claims
- Application Information
AI Technical Summary
Benefits of technology
Problems solved by technology
Method used
Image
Examples
example 1
[0170]
[0171]80 parts by mass of EPDM: MITSUI EPT1045 (ethylene-propylene-diene copolymer, ethylene content: 58% by mass, diene content: 5% by mass, kind of diene: dicyclopentadiene (DCPD), manufactured by Mitsui Chemicals, Inc.) as a polymer, 12 parts by mass of carbon black #45L (nitrogen adsorption specific surface area: 125 m2 / g, DBP absorption: 45 cm3 / 100 g, manufactured by Mitsubishi Chemical Corporation.) as a photothermal converting agent, and 5 parts by mass of PERCUMYL D40 (dicumyl peroxide (40% by mass), manufactured by NOF CORPORATION) were kneaded to prepare a resin composition A. In the following first table, the formulation using the resin composition A is expressed as “Formulation A”, and cases of using resin compositions B to F described later are expressed as “Formulations B to F” respectively.
[0172]
[0173]The obtained resin composition A was crosslinked by heating at a pressure of 10 MPa and 160° C. for 20 minutes using a heating press machine (MP-WCL, manufactured
example 14
[0182]A flexographic printing plate was manufactured in the same manner as in Example 1except that as the recessed portion forming pattern, instead of Pattern I, Pattern II was used.
example 15
[0183]A flexographic printing plate was manufactured in the same manner as in Example 1 except that as the recessed portion forming pattern, instead of Pattern I, Pattern III was used.
PUM
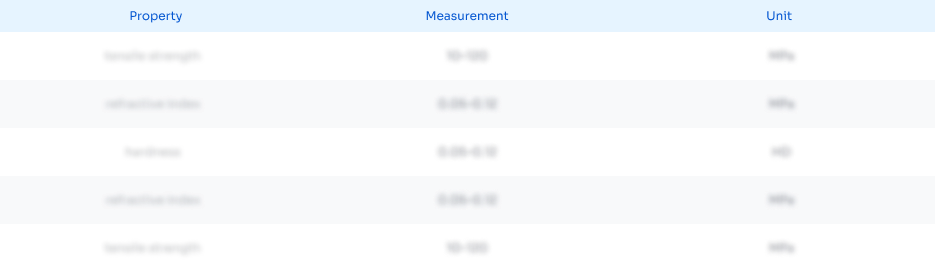
Abstract
Description
Claims
Application Information
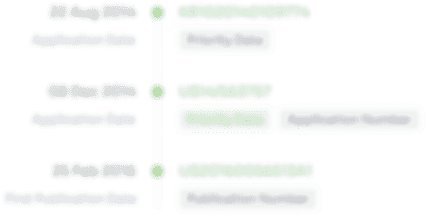
- R&D Engineer
- R&D Manager
- IP Professional
- Industry Leading Data Capabilities
- Powerful AI technology
- Patent DNA Extraction
Browse by: Latest US Patents, China's latest patents, Technical Efficacy Thesaurus, Application Domain, Technology Topic.
© 2024 PatSnap. All rights reserved.Legal|Privacy policy|Modern Slavery Act Transparency Statement|Sitemap