Ink composition and container
a technology of composition and ink, applied in the field of ink composition and container, can solve the problems of insufficient stability of continuous printing, reduced resin particle content of ink composition, and difficulty in producing excellent fastness of recorded matters, and achieve excellent fastness
- Summary
- Abstract
- Description
- Claims
- Application Information
AI Technical Summary
Benefits of technology
Problems solved by technology
Method used
Image
Examples
production example 1
[0079]Into a reaction vessel equipped with a stirrer, a reflux condenser, a dropping device, and a thermometer, 900 g of ion exchanged water and 3 g of sodium lauryl sulfate were put. The content was heated to 70° C. under stirring while the inside of the reaction vessel was purged with nitrogen. Then, 4 g of potassium persulfate as a polymerization initiator was added thereto and dissolved while the internal temperature was maintained to be 70° C.; and an emulsion preliminarily prepared by adding 20 g of acrylamide, 300 g of styrene, 640 g of butylacrylate, and 30 g of methacrylic acid to 450 g of ion exchanged water and 3 g of sodium lauryl sulfate under stirring was subsequently continuously dropped to the reaction solution over 4 hours. After the dropping, the resulting product was aged over three hours. The resulting aqueous emulsion was cooled to normal temperature, and then ion exchanged water and an aqueous solution of 5% sodium hydroxide were added thereto to adjust the solid
production example 2
[0080]Into a reaction vessel equipped with a stirrer, a reflux condenser, a dropping device, and a thermometer, 900 g of ion exchanged water and 1 g of sodium lauryl sulfate were put. The content was heated to 70° C. under stirring while the inside of the reaction vessel was purged with nitrogen. Then, 4 g of potassium persulfate as a polymerization initiator was added thereto and dissolved while the internal temperature was maintained to be 70° C.; and an emulsion preliminarily prepared by adding 20 g of acrylamide, 365 g of styrene, 545 g of butylacrylate, and 30 g of methacrylic acid to 450 g of ion exchanged water and 3 g of sodium lauryl sulfate under stirring was subsequently continuously dropped to the reaction solution over 4 hours. After the dropping, the resulting product was aged over three hours. The resulting aqueous emulsion was cooled to normal temperature, and then ion exchanged water and an aqueous solution of sodium hydroxide were added thereto to adjust the solid con
production example 3
[0081]Into a reaction vessel equipped with a stirrer, a reflux condenser, a dropping device, and a thermometer, 900 g of ion exchanged water and 1 g of sodium lauryl sulfate were put. The content was heated to 70° C. under stirring while the inside of the reaction vessel was purged with nitrogen. Then, 4 g of potassium persulfate as a polymerization initiator was added thereto and dissolved while the internal temperature was maintained to be 70° C.; and an emulsion preliminarily prepared by adding 20 g of acrylamide, 615 g of styrene, 295 g of butylacrylate, and 30 g of methacrylic acid to 450 g of ion exchanged water and 3 g of sodium lauryl sulfate under stirring was subsequently continuously dropped to the reaction solution over 4 hours. After the dropping, the resulting product was aged over three hours. The resulting aqueous emulsion was cooled to normal temperature, and then ion exchanged water and an aqueous solution of sodium hydroxide were added thereto to adjust the solid con
PUM
Property | Measurement | Unit |
---|---|---|
Fraction | aaaaa | aaaaa |
Percent by mass | aaaaa | aaaaa |
Percent by mass | aaaaa | aaaaa |
Abstract
Description
Claims
Application Information
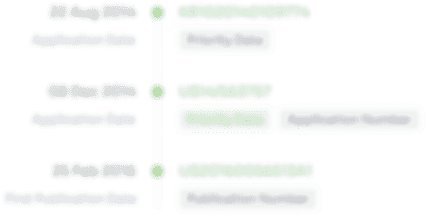
- R&D Engineer
- R&D Manager
- IP Professional
- Industry Leading Data Capabilities
- Powerful AI technology
- Patent DNA Extraction
Browse by: Latest US Patents, China's latest patents, Technical Efficacy Thesaurus, Application Domain, Technology Topic.
© 2024 PatSnap. All rights reserved.Legal|Privacy policy|Modern Slavery Act Transparency Statement|Sitemap