Pneumatic cylinder with safety device
a safety device and pneumatic cylinder technology, applied in the direction of forging presses, shock absorbers, elastic dampers, etc., can solve problems such as piston-rod breakage, and achieve the effects of increasing safety, reducing friction, and reducing friction
- Summary
- Abstract
- Description
- Claims
- Application Information
AI Technical Summary
Benefits of technology
Problems solved by technology
Method used
Examples
Embodiment Construction
[0023]FIG. 1 contains a schematic view of a press 1, wherein the press 1 comprises a press frame 2 with header 3, supports 4, 5 and press table 6. A ram 7 is positioned above the press table 6, between the supports 4, 5, which ram can move vertically up and down as indicated by arrow 8. The ram 7 is operated by a main press drive that is connected via driving rods 9, 11 to the ram 7. To take a load off the main press drive, one or several weight-balancing devices 12, 13, which generate a pulling force in an upward direction, are assigned to the ram 7. This force is introduced into the ram 7 via piston rods 14, 15 that function as pull rods while the weight-balancing devices 12, 13 support themselves on the press frame 2. Other force-transmitting devices such a pipes or pulling means can also be used in place of the piston rods 14, 15.
[0024]The following description of the weight-balancing device 12 applies in the same way to the weight-balancing device 13:
[0025]FIG. 2 shows the weig...
PUM
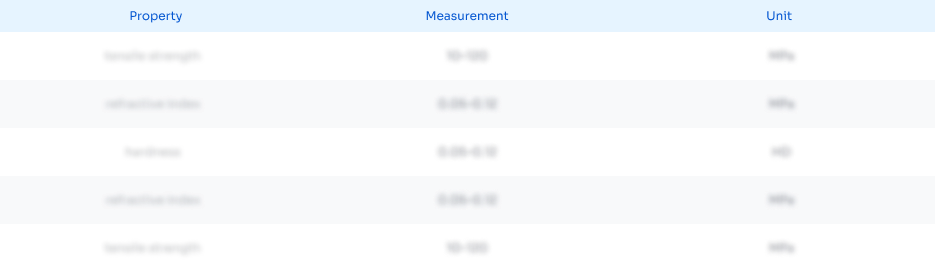
Abstract
Description
Claims
Application Information
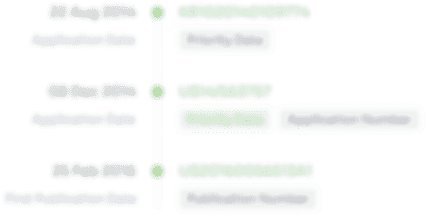
- R&D Engineer
- R&D Manager
- IP Professional
- Industry Leading Data Capabilities
- Powerful AI technology
- Patent DNA Extraction
Browse by: Latest US Patents, China's latest patents, Technical Efficacy Thesaurus, Application Domain, Technology Topic.
© 2024 PatSnap. All rights reserved.Legal|Privacy policy|Modern Slavery Act Transparency Statement|Sitemap