Vehicle braking system with proportional poppet valve pressure control strategy
- Summary
- Abstract
- Description
- Claims
- Application Information
AI Technical Summary
Benefits of technology
Problems solved by technology
Method used
Image
Examples
Example
[0022]Referring now to the drawings, there is illustrated in FIG. 1 a portion 10 of the electronic circuitry processing braking signals that implements a pressure control algorithm according to the present invention, together with a greatly simplified schematic representation of a typical EHB system 12. A more detailed description of an EHB system for which the algorithm of the present invention may suitably be used is described in U.S. Pat. No. 5,941,608 to Campau et al., the disclosure of which is hereby incorporated by reference. However, it should be understood that it is believed that the present invention may suitably be practiced in a variety of other EHB systems, including without limitation, the EHB system described in the SAE Technical Paper Series No. 950762, “Intelligent Braking for Current and Future Vehicles”, and No. 960991, “Electrohydraulic Brake System—The First Approach to Brake-By-Wire Technology”, the disclosures of which are also incorporated by reference. It shou
PUM
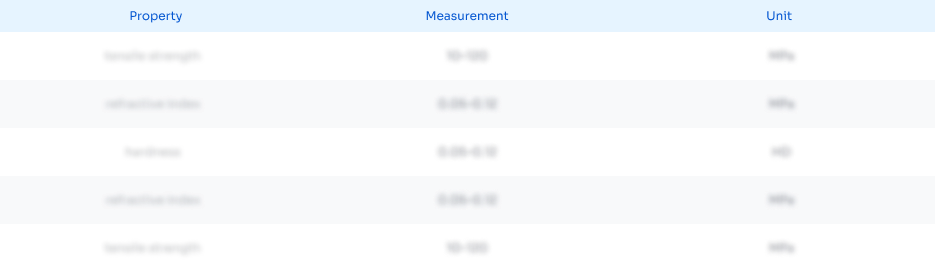
Abstract
Description
Claims
Application Information
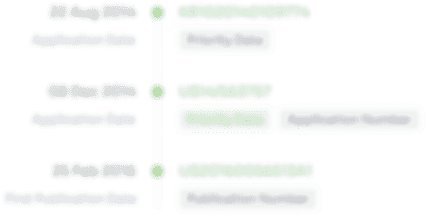
- R&D Engineer
- R&D Manager
- IP Professional
- Industry Leading Data Capabilities
- Powerful AI technology
- Patent DNA Extraction
Browse by: Latest US Patents, China's latest patents, Technical Efficacy Thesaurus, Application Domain, Technology Topic.
© 2024 PatSnap. All rights reserved.Legal|Privacy policy|Modern Slavery Act Transparency Statement|Sitemap