Optical block assembly
a technology of optical blocks and assemblies, applied in the field of optical block assemblies, can solve the problems of increased rotational speeds, limited image sensor size, and rotational inertia of longer optical blocks, and achieve the effects of reducing cctv camera applications, reducing angular inertia, and compactness
- Summary
- Abstract
- Description
- Claims
- Application Information
AI Technical Summary
Benefits of technology
Problems solved by technology
Method used
Image
Examples
Embodiment Construction
[0031]FIGS. 2A, 2B and 3A illustrate respective side, frontal and perspective views of one exemplary embodiment of a multiple stage folded light path optical block assembly according to the disclosed systems and methods. In this regard, FIGS. 2A, 2B and 3 illustrate a dual-stage folded light path optical block assembly 200 that includes an optical block housing 202 that maintains in operative relationship a pair of 90-degree reflecting prisms 218 and 220, a movable zoom lens assembly 206, a movable focus lens assembly 207 and image sensor circuit board assembly 210. As illustrated, prisms 218 and 220 are operatively disposed to form an optical path between a light or image gathering lens 204 and an image sensor 208 of assembly 200.
[0032]Still referring to FIGS. 2A, 2B and 3A, light gathering lens 204 is configured to provide a first or initial linear light path defined between light gathering lens 204 at front end 230 of assembly 200 and first 90-degree reflecting prism 218. As shown,
PUM
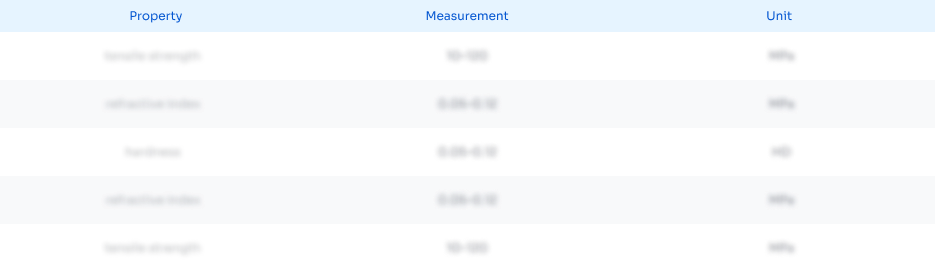
Abstract
Description
Claims
Application Information
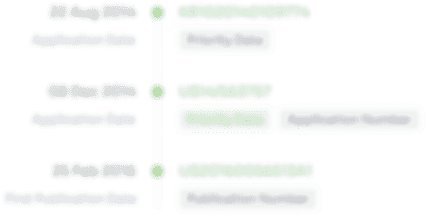
- R&D Engineer
- R&D Manager
- IP Professional
- Industry Leading Data Capabilities
- Powerful AI technology
- Patent DNA Extraction
Browse by: Latest US Patents, China's latest patents, Technical Efficacy Thesaurus, Application Domain, Technology Topic.
© 2024 PatSnap. All rights reserved.Legal|Privacy policy|Modern Slavery Act Transparency Statement|Sitemap