Process for the gas phase polymerisation of olefins
- Summary
- Abstract
- Description
- Claims
- Application Information
AI Technical Summary
Benefits of technology
Problems solved by technology
Method used
Examples
Example
Example 1
Metallocene Catalyst
[0087]In a first set of experiments, a metallocene catalyst was simulated using ethylene and 1-hexene, in the presence of hydrogen, to produce a polyethylene having a density of 918 kg / m3 and a melt index of 3.5 g / 10 min.
[0088]The reactor conditions were selected for two different production rates. As a comparative example, the process was simulated at a production rate of 30 tonnes / hour, corresponding to a space-time yield (STY) of 57 kg / hr / m3. A condensation rate of 7.3 wt % was used. Under these conditions the ratio of hydrogen:ethylene at the top of the fluidised bed compared to the ratio of hydrogen:ethylene at the base of the fluidised bed was 1.022 i.e. there was a 2% difference in the ratio. (A value of 1 indicates the same ratio of components at both the top and base of the fluidised bed). Similarly, the ratio of 1-hexene:ethylene at the top of the fluidised bed compared to the ratio of 1-hexene:ethylene at the base of the fluidised bed w
Example
Example 2
Ziegler-Natta Catalyst
[0090]In a second set of simulations, a Ziegler-Natta catalyst was used to react ethylene and 1-hexene, in the presence of hydrogen, to produce a polyethylene having a density of 936 kg / m3, melt index of 0.9 g / 10 min.
[0091]The reactor was again operated at two different production rates. As a comparative example, the process was operated at a production rate of 30 tonnes / hour, corresponding to a space-time yield (STY) of 57 kg / hr / m3. A condensation rate of 1 wt % was used. Under these conditions the ratio of hydrogen:ethylene at the top of the fluidised bed compared to the ratio of hydrogen:ethylene at the base of the fluidised bed was 1.05 i.e. there was a 5% difference in the ratio. Similarly, the ratio of 1-hexene:ethylene at the top of the fluidised bed compared to the ratio of 1-hexene:ethylene at the base of the fluidised bed was 1.04 i.e. there was a 4% increase in the ratio.
[0092]Whilst not insignificant, under these conditions a uniform
Example
Example 3
Ziegler-Natta Catalyst
[0093]In a third set of simulations, a Ziegler-Natta catalyst was again used to react ethylene and 1-hexene, in the presence of hydrogen, this time to produce a polyethylene having a density of 918 kg / m3, melt index 3 g / 10 min.
[0094]The reactor was again simulated at two different production rates. As a comparative example, the process was simulated at a production rate of 30 tonnes / hour. No condensation was used. Under these conditions the ratio of hydrogen:ethylene at the top of the fluidised bed compared to the ratio of hydrogen:ethylene at the base of the fluidised bed was 1.115 i.e. there was an 11.5% difference in the ratio. Similarly, the ratio of 1-hexene:ethylene at the top of the fluidised bed compared to the ratio of 1-hexene:ethylene at the base of the fluidised bed was 1.025 i.e. there was a 2.5% increase in the ratio. Whilst not insignificant, under these conditions a uniform operation was obtained.
[0095]The production rate was then si
PUM
Property | Measurement | Unit |
---|---|---|
Mass flow rate | aaaaa | aaaaa |
Pressure | aaaaa | aaaaa |
Pressure drop | aaaaa | aaaaa |
Abstract
Description
Claims
Application Information
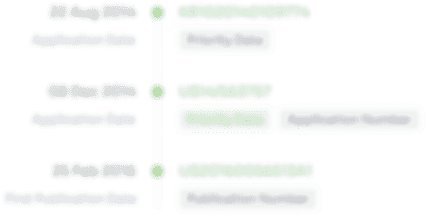
- R&D Engineer
- R&D Manager
- IP Professional
- Industry Leading Data Capabilities
- Powerful AI technology
- Patent DNA Extraction
Browse by: Latest US Patents, China's latest patents, Technical Efficacy Thesaurus, Application Domain, Technology Topic.
© 2024 PatSnap. All rights reserved.Legal|Privacy policy|Modern Slavery Act Transparency Statement|Sitemap