Method for recasting and reforming molded water-base casting film
A water-based casting and casting molding technology, applied in the field of casting molding technology, can solve the problems of recycling and utilization of water-based casting films, and achieve universality, easy control of conditions, cost and resource reduction. wasteful effect
- Summary
- Abstract
- Description
- Claims
- Application Information
AI Technical Summary
Problems solved by technology
Method used
Examples
Example Embodiment
[0019] Example 1
[0020] 100g of Al with an average particle size of 400nm 2 O 3 The powder was added to 25ml of water containing 2.0g of dispersant potassium polyacrylate (PAA-K) and ball milled for 24h. Add 50g of 12wt% PVA solution and 7.2g of 1,2-propanediol. Among them, the binder of the slurry / ceramic powder (X=0.06), plasticizer / binder (Y=1.2), (ceramic powder+binder+plasticizer) / solvent water (Z=1.64) . Continue ball milling for 24h, the obtained slurry η 0 =600mPa·s. The slurry is vacuum degassed and then cast to shape, and a cast film is obtained after natural drying.
[0021] Put part of the cast film into a container, add a certain amount of water, and dissolve the cast film under strong stirring at 90-100°C. After cooling to room temperature, ball mill for 12 hours to obtain a secondary slurry, and measure its viscosity η 1 =600mPa·s. The secondary slurry is vacuum degassed and then cast into a shape with a vacuum degree of 600-1000torr. After natural drying, a se
Example Embodiment
[0022] Example 2
[0023] 100g of Al with an average particle size of 400nm 2 O 3 The powder was added to 25ml of water containing 2.0g of dispersant potassium polyacrylate (PAA-K) and ball milled for 24h. Add 50g of 12wt% PVA solution and 7.2g of 1,2-propanediol. Among them, the binder of the slurry / ceramic powder (X=0.06), plasticizer / binder (Y=1.2), (ceramic powder+binder+plasticizer) / solvent water (Z=1.64) . Continue ball milling for 24h, the obtained slurry η 0 =600mPa·s. The slurry is vacuum degassed and then cast into shape. The vacuum degassing time is 30 minutes. After natural drying, a cast film is obtained.
[0024] Put part of the cast film into a container, add a certain amount of water, and dissolve the cast film under strong stirring at 90-100°C. After cooling to room temperature, ball mill for 12 hours to obtain a secondary slurry, and measure its viscosity η 1 =580mPa·s. The secondary slurry is vacuum degassed and then cast into shape, and then naturally dried
Example Embodiment
[0025] Example 3
[0026] 100g of Al with an average particle size of 400nm 2 O 3 The powder was added to 25ml of water containing 2.0g of dispersant potassium polyacrylate (PAA-K) and ball milled for 24h. 58.3g of 12wt% PVA solution and 7.0g of 1,2-propanediol were added. Among them, the binder of the slurry / ceramic powder (X=0.07), plasticizer / binder (Y=1.0), (ceramic powder+binder+plasticizer) / solvent water (Z=1.49) . Continue ball milling for 24h, the obtained slurry η 0 =770mPa·s. The slurry is vacuum degassed and then cast to shape, and a cast film is obtained after natural drying.
[0027] Put part of the cast film into a container, add a certain amount of water, and dissolve the cast film under vigorous stirring at 90-100°C. After cooling to room temperature, ball mill for 24 hours to obtain a secondary slurry and measure its viscosity η 1 =760mPa·s. The secondary slurry is vacuum degassed and then cast into shape, and then naturally dried to obtain a secondary cast fil
PUM
Property | Measurement | Unit |
---|---|---|
Particle size | aaaaa | aaaaa |
The average particle size | aaaaa | aaaaa |
Abstract
Description
Claims
Application Information
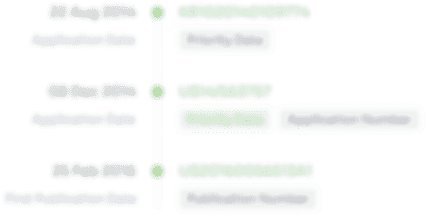
- R&D Engineer
- R&D Manager
- IP Professional
- Industry Leading Data Capabilities
- Powerful AI technology
- Patent DNA Extraction
Browse by: Latest US Patents, China's latest patents, Technical Efficacy Thesaurus, Application Domain, Technology Topic.
© 2024 PatSnap. All rights reserved.Legal|Privacy policy|Modern Slavery Act Transparency Statement|Sitemap