Shell-and-tube type heat exchanger employing crossed spiral tube
A technology of shell-and-tube heat exchangers and spiral tubes, which can be used in exhaust gas recirculation heat exchangers, exhaust attachments, and engine inlets. It can solve the problems of low heat exchange efficiency and achieve improved heat exchange effects and good exhaust gas. Use the effect of the effect
- Summary
- Abstract
- Description
- Claims
- Application Information
AI Technical Summary
Benefits of technology
Problems solved by technology
Method used
Image
Examples
Embodiment 1
[0022] 1 and 2 are respectively a three-dimensional structural schematic diagram and a cross-sectional schematic diagram at the tube sheet of the first embodiment of the present invention. The serial numbers in the figure represent: 1. Shell, 2. Heat exchange tube, 3. Tube sheet, 4. Exhaust gas inlet and outlet, 5. Baffle plate. Figure 1 is a schematic diagram of an arrangement of flat cross-helical tubes in a U-shaped tube heat exchanger. One end of the shell 1 is provided with an opening, and a tube plate 3 is provided at the opening, and the two ends of the U-shaped heat exchange tube 2 (ie, the exhaust gas inlet end and the exhaust gas outlet end 4) are assembled on the same side of the tube plate; There is a through hole for fixing the U-shaped heat exchange tube on the end surface of the joint of the exhaust gas inlet and outlet 4; the heat exchange tube 2 is composed of two straight pipe sections and one bent pipe section, and is in a U-shape. The two ends of the U-shaped
Embodiment 2
[0031] Fig. 5 is a sectional view of the heat exchange tube in this embodiment. The difference between this embodiment and the embodiment described in FIG. 4 above is that the cross-sectional shape of the stainless steel pipe body is flat, the two opposite long sides are straight lines, and the relatively short sides are arc-shaped convex semicircular arc surfaces from the inside to the outside. Such a setting can improve heat exchange efficiency.
[0032] The flat spiral heat exchange tube arranged in the exhaust gas recirculation cooler not only increases the heat exchange area compared with the circular tube, but also strengthens the disturbance of the fluid in the tube. Because the flat tube is not symmetrical to the center of the round tube, the distance between the geometric center of the flat spiral tube and the tube wall is smaller than the distance between the circular spiral tube and the tube wall, and most of the fluid in the tube can participate in heat exchange , an
Embodiment 3
[0034] Fig. 6 is a sectional view of the heat exchange tube in this embodiment. This embodiment is a modification based on the embodiment described in Figure 4 above, and the entire cross-section of the heat exchange tubes is connected smoothly, that is, for the convenience of processing, when the cross-sectional shape of the spiral groove is removed, the The cross-sectional shape of the pipe body is set to an ellipse;
PUM
Property | Measurement | Unit |
---|---|---|
Helix angle | aaaaa | aaaaa |
Depth | aaaaa | aaaaa |
Abstract
Description
Claims
Application Information
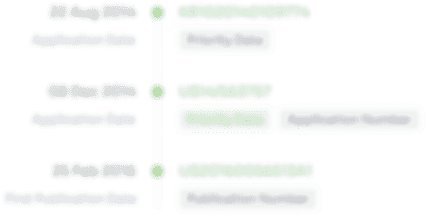
- R&D Engineer
- R&D Manager
- IP Professional
- Industry Leading Data Capabilities
- Powerful AI technology
- Patent DNA Extraction
Browse by: Latest US Patents, China's latest patents, Technical Efficacy Thesaurus, Application Domain, Technology Topic.
© 2024 PatSnap. All rights reserved.Legal|Privacy policy|Modern Slavery Act Transparency Statement|Sitemap