Making method for compound electric heating plate
A manufacturing method and technology of electric heating plate, applied in the direction of heating element materials, etc., can solve the problems of inconvenient installation, restricted use, hidden dangers in use, etc., and achieve the effect of improving the effect of heat insulation, tight fit, and eliminating gaps.
- Summary
- Abstract
- Description
- Claims
- Application Information
AI Technical Summary
Problems solved by technology
Method used
Image
Examples
Embodiment 1
[0021] Take YKB-613 (product model) as an example, the overall size is 640*940*15mm, and the rated power is 120W. Main production materials: side strips (plywood), insulation layer (polyurethane rigid foam, flame retardant), electric heating film (carbon crystal electric heating film), etc. As shown in Figure 1, its production process is as follows:
[0022] 1. Lath processing
[0023] 1.1 Use a panel saw to process ordinary plywood with a thickness of 12mm and 3mm into planks of predetermined specifications.
[0024] 1.2 Slat assembly: Bind the slats of the above specifications into frames of predetermined specifications with horse nails.
[0025] 2. Carbon crystal electric heating film welding wire
[0026] 2.1 Grinding the solder joints of the lead wires of the carbon crystal electric heating film.
[0027] 2.2 Solder the 30mm long red and black wires to the polished solder joints.
[0028] 3. Molding
[0029] 3.1 First put the frame bound in step 1 into the aluminum all
Embodiment 2
[0046] Take YKB-613 (product model) as an example, the overall size is 640*940*16mm, and the rated power is 120W. Other manufacturing processes are the same as in Example 1, except that a layer of high surface density polyethylene (HDPE) plastic sheet is pasted on the carbon crystal electric heating film to improve the waterproof and moisture-proof performance and insulation of the composite board. See Figure 1 for details, namely Only after trimming in step 5 and before pasting the logo, a step of applying glue and pasting the plastic sheet is added:
[0047] 1. In step 5.1, use a utility knife to cut off the excess kraft paper, clean up the foam material leaking from the slats, and proceed to the next step;
[0048] 2. Glue application: apply the self-adhesive evenly on the carbon crystal surface with a special roller, and the amount of glue applied is 50-150g / sheet;
[0049] 3. Airing: Place the carbon crystal electric heating plate coated with glue on the airing rack for a
Embodiment 3
[0055] The other manufacturing processes are the same as in Examples 1 and 2, except that the kraft paper is replaced with aluminum foil paper in step 3.3, which not only beautifies the appearance of the product, but also improves the product grade, and the aluminum foil paper also strengthens the far-infrared radiation function of the electric heating plate.
PUM
Property | Measurement | Unit |
---|---|---|
Density | aaaaa | aaaaa |
Thickness | aaaaa | aaaaa |
Density | aaaaa | aaaaa |
Abstract
Description
Claims
Application Information
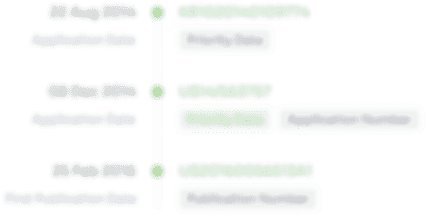
- R&D Engineer
- R&D Manager
- IP Professional
- Industry Leading Data Capabilities
- Powerful AI technology
- Patent DNA Extraction
Browse by: Latest US Patents, China's latest patents, Technical Efficacy Thesaurus, Application Domain, Technology Topic.
© 2024 PatSnap. All rights reserved.Legal|Privacy policy|Modern Slavery Act Transparency Statement|Sitemap