Production process of hollow glass
A production process and glass technology, applied in the field of insulating glass production process, can solve the problems of inconvenient production management, high production cost, low production efficiency, etc., and achieve the effects of improving production efficiency, saving costs, and being easy to detect and maintain
- Summary
- Abstract
- Description
- Claims
- Application Information
AI Technical Summary
Benefits of technology
Problems solved by technology
Method used
Image
Examples
Embodiment Construction
[0009] like figure 1 As shown, the hollow glass production process described in the embodiment of the present invention includes the following steps: the glass to be processed is first sent to the cleaning and drying machine through the glass conveyor, and the glass passes through the brush, rubber roller, nozzle and fan on this equipment. After being cleaned and dried, the end of the glass conveyor is equipped with a sensor that automatically recognizes the layer of the coated glass film. When the production personnel mistakenly places the layer of the glass film incorrectly, the rubber roller motor of the cleaning machine will automatically stop running, and the touch screen will display the coated glass layer. Identify abnormalities in the system; then check whether the surface of the glass is clean by checking the conveyor, which is equipped with a rotary encoder and sensor signals; when the first piece of glass enters the frame machine, the required aluminum can be pasted st
PUM
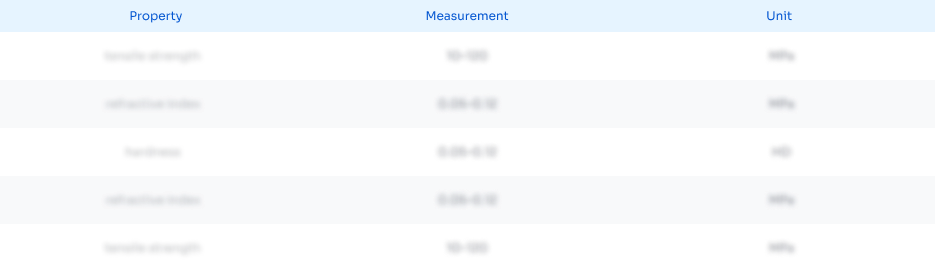
Abstract
Description
Claims
Application Information
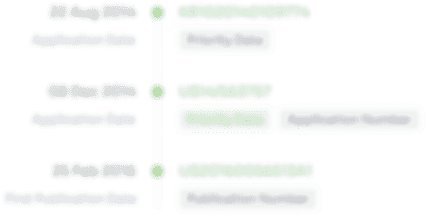
- R&D Engineer
- R&D Manager
- IP Professional
- Industry Leading Data Capabilities
- Powerful AI technology
- Patent DNA Extraction
Browse by: Latest US Patents, China's latest patents, Technical Efficacy Thesaurus, Application Domain, Technology Topic.
© 2024 PatSnap. All rights reserved.Legal|Privacy policy|Modern Slavery Act Transparency Statement|Sitemap