Method for measuring temperatures of out-flowing water and discharged water of heater of turbine steam cooler
A steam cooler and steam cooling technology, which is used in feedwater heaters, steam generation, steam engine installations, etc., can solve the problems of high measurement cost, inability to calculate heat transfer coefficient, inconvenient maintenance and maintenance, etc.
- Summary
- Abstract
- Description
- Claims
- Application Information
AI Technical Summary
Problems solved by technology
Method used
Image
Examples
Embodiment Construction
[0062] A method for measuring and calculating the outlet water and drain temperature of a heater with a steam cooler in a steam turbine, characterized in that,
[0063] Step 1: Calculate the intermediate transition point temperature t between the steam cooling section and the pure condensation section of the heater under the reference condition wsj o :
[0064] Select the rated power design condition of the unit or the performance assessment test condition as the reference condition, and the parameters with the letter "o" added to the symbol indicate that it is a parameter under the reference condition, and select the j-th stage heater under the reference condition Thermal parameters: shell side pressure p nj o , Extraction temperature t j o , shell side extraction enthalpy h nj o , outlet water temperature t wj o , Inlet water temperature t w(j+1) o and unit power P e o , and according to the IAPWS-IF97 industrial water and steam thermodynamic properties model to ca
PUM
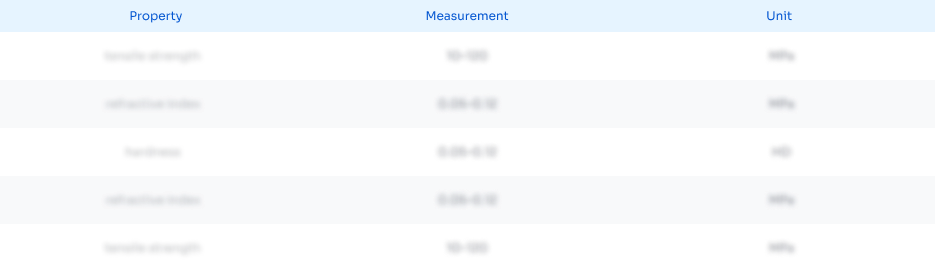
Abstract
Description
Claims
Application Information
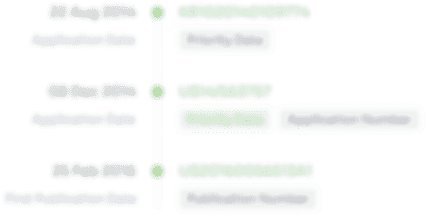
- R&D Engineer
- R&D Manager
- IP Professional
- Industry Leading Data Capabilities
- Powerful AI technology
- Patent DNA Extraction
Browse by: Latest US Patents, China's latest patents, Technical Efficacy Thesaurus, Application Domain, Technology Topic.
© 2024 PatSnap. All rights reserved.Legal|Privacy policy|Modern Slavery Act Transparency Statement|Sitemap