Method for relieving pattern segregation of spring steel
A technology of ingot segregation and spring steel is applied in the field of improving spring steel ingot segregation to achieve the effect of reducing production costs
- Summary
- Abstract
- Description
- Claims
- Application Information
AI Technical Summary
Benefits of technology
Problems solved by technology
Method used
Image
Examples
Embodiment 1
[0023] 1. Conventional smelting, control the temperature of the upper continuous casting platform. During continuous casting, the temperature of the tundish is controlled at the liquidus line of 28°C, and the casting speed is controlled at 0.5m / min. 320*420mm bloom, the current intensity is 450A, the frequency is 2Hz; the end liquid core is lightly pressed down by 5mm.
[0024] 2. The process of forming billet into 185*185mm billet by the second fire: the heating process is the temperature of the first heating section: 996°C, the temperature of the second heating section: 1249°C, the temperature of the soaking section: 1212°C, and the time of the second heating section and soaking section is 196min; The billet stays in the furnace for 238 minutes; the furnace pressure is maintained at a slightly positive pressure, and the atmosphere in the furnace is maintained at a weakly reducing atmosphere; the rolling start temperature is 1111°C, the reductions in the first three passes are
Embodiment 2
[0028] 1. Conventional smelting, control the temperature of the upper continuous casting platform. During continuous casting, the tundish temperature is controlled at the liquidus line of 33°C, and the casting speed is controlled at 0.3m / min. 320*420mm bloom, the current intensity is 300A, the frequency is 2Hz; the liquid core at the end is lightly pressed down by 5mm.
[0029] 2. The process of making billets into 185*185mm square billets with the second fire: the heating process is the temperature of the first heating section: 1089°C, the temperature of the second heating section: 1247°C, the temperature of the soaking section: 1238°C, and the time of the second heating section and soaking section is 183min; The billet stays in the furnace for 225 minutes; the furnace pressure is maintained at a slightly positive pressure, and the atmosphere in the furnace is maintained at a weakly reducing atmosphere; the rolling start temperature is 1133°C, the reductions in the first three
Embodiment 3
[0033] 1. Conventional smelting, control the temperature of the upper continuous casting platform. During continuous casting, the tundish temperature is controlled at the liquidus line of 30°C, and the casting speed is controlled at 0.4m / min. 320*420mm bloom, the current intensity is 360A, the frequency is 2Hz; the end liquid core is lightly pressed down by 5mm.
[0034] 2. The process of forming billet into 185*185mm billet by the second fire: the heating process is the temperature of the first heating section: 959°C, the temperature of the second heating section: 1213°C, the temperature of the soaking section: 1243°C, and the time of the second heating section and soaking section is 201min; The billet was in the furnace for 239 minutes; the furnace pressure was maintained at a slightly positive pressure, and the atmosphere in the furnace was maintained at a weakly reducing atmosphere; the rolling start temperature was 1134°C, and the reductions in the first three passes were c
PUM
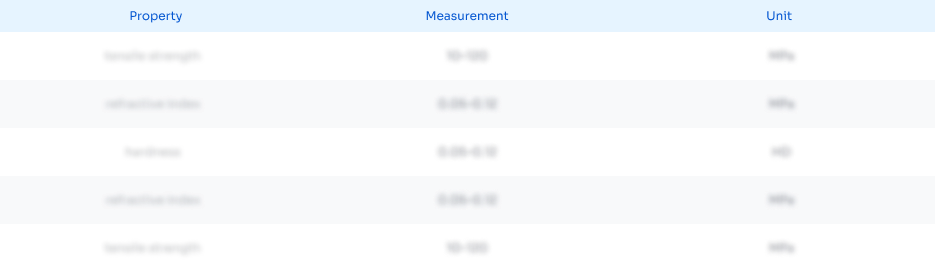
Abstract
Description
Claims
Application Information
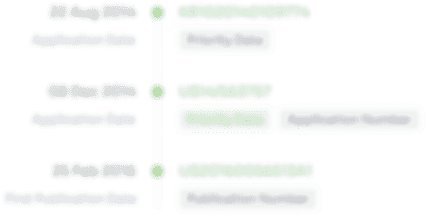
- R&D Engineer
- R&D Manager
- IP Professional
- Industry Leading Data Capabilities
- Powerful AI technology
- Patent DNA Extraction
Browse by: Latest US Patents, China's latest patents, Technical Efficacy Thesaurus, Application Domain, Technology Topic.
© 2024 PatSnap. All rights reserved.Legal|Privacy policy|Modern Slavery Act Transparency Statement|Sitemap