Production technology of wire rod for solid surfacing welding wires
A technology for surfacing welding wire and production process, which is applied in welding media, manufacturing tools, welding equipment, etc., can solve the problem of high cost, and achieve the effect of low production cost, high deposition and welding efficiency, and easy automatic operation.
- Summary
- Abstract
- Description
- Claims
- Application Information
AI Technical Summary
Problems solved by technology
Method used
Image
Examples
Embodiment 1
[0027] Converter process: use high carbon and dephosphorization organic combination, control the end point C=0.15%, P=0.010%, in the early stage of blowing, use large bottom blowing and stirring to achieve the purpose of rapid dephosphorization; adjust the oxygen lance height 1.3-1.8 m, rapid slag removal; medium-intensity bottom blowing is used in the middle and later stages to prevent slag from drying out and molten steel returning to P; control the basicity of slag at 2.5, and softly blow argon for 3 minutes after the furnace; control the end point temperature to 1620°C; use SiAlBa composite deoxidizer for deoxidation , the dosage is 1.0; the temperature from the molten steel to the LF refining station is 1540°C;
[0028] LF refining process: blow argon after entering the station, add refining slag and reducing agent in batches, quickly supply electricity to form white slag, ensure white slag refining time 20min, feed φ13mm CaSi wire 80m after the composition and temperature...
Embodiment 2
[0037] Converter process: use high-strength carbon and dephosphorization organically, control the end point C=0.18%, P=0.009%, use large bottom blowing and stirring in the early stage of blowing to achieve the purpose of rapid dephosphorization; adjust the height of the oxygen lance to 1.5m, Rapid slag removal; medium-intensity bottom blowing is used in the middle and later stages to prevent the slag from drying out and molten steel returning to P; the basicity of the slag is controlled at 2.8, and argon is blown softly after the furnace for 4 minutes; the end point temperature is controlled at 1640°C; the SiAlBa composite deoxidizer is used for deoxidation. 1.3kg / t; the target temperature of molten steel to LF refining station is 1570℃;
[0038] Refining process: blow argon after entering the station, add refining slag and reducing agent in batches, quickly supply electricity to form white slag, ensure white slag refining time 25 minutes, feed φ13mm CaSi wire 95m after the com...
Embodiment 3
[0047] Converter process: use high carbon and dephosphorization organic combination, control the end point C=0.20%, P=0.010%, adjust the oxygen lance height to 1.8m, and quickly melt slag; use large bottom blowing and stirring in the early stage of blowing to achieve rapid dephosphorization The purpose of this method is to use medium-intensity bottom blowing in the middle and late stages to prevent the slag from drying out and the molten steel to return to P; control the basicity of the slag at 3.0, and blow argon softly after the furnace for 5 minutes; control the end point temperature to 1650 ° C, and use SiAlBa composite deoxidizer for deoxidation, with a dosage of 1.5 kg / t; the temperature from molten steel to LF refining station is 1560℃;
[0048] LF refining process: blow argon after entering the station, add refining slag and reducing agent in batches, quickly supply electricity to form white slag, ensure white slag refining time 28 minutes, feed 100m of φ13mm CaSi wire ...
PUM
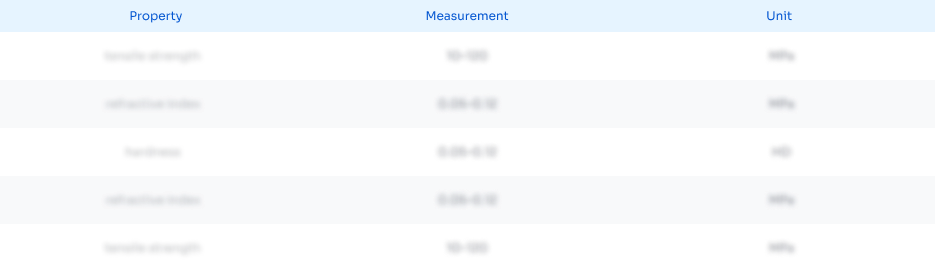
Abstract
Description
Claims
Application Information
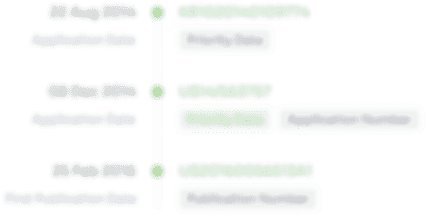
- R&D Engineer
- R&D Manager
- IP Professional
- Industry Leading Data Capabilities
- Powerful AI technology
- Patent DNA Extraction
Browse by: Latest US Patents, China's latest patents, Technical Efficacy Thesaurus, Application Domain, Technology Topic.
© 2024 PatSnap. All rights reserved.Legal|Privacy policy|Modern Slavery Act Transparency Statement|Sitemap