Deep navy reactive dye fixing agent and production process thereof
A technology of reactive dyes and production technology, applied in dyeing, organic dyes, textiles and papermaking, etc., can solve the problems of high cost, high consumption, and soda ash not conforming to the production process, and achieve low production cost and less pollution
- Summary
- Abstract
- Description
- Claims
- Application Information
AI Technical Summary
Benefits of technology
Problems solved by technology
Method used
Image
Examples
Embodiment 1
[0012] Take a package of yarn, add 1.8g of dyes AEL Yellow, 26g of AEL Claret, 139g of AEL Zhangqing, add 40kg of water to mix, add 3170g of Yuanmingfen at room temperature, then heat to 40°C, and wait 15 minutes after the temperature reaches 40°C Add 198g of soda ash, add 59g of caustic soda after another 15 minutes, wait for 50 minutes and then wash with water and soap.
Embodiment 2
[0014] Take a package of yarn, add 2.2g of dyes AEL Yellow, 28g of AEL Claret, 141g of AEL Zhangqing, add 40kg of water to mix, add 3230g of Yuanmingfen at room temperature, then heat to 40°C, and wait 15 minutes after the temperature reaches 40°C Add 202g of soda ash, add 61g of caustic soda after another 15 minutes, wait for 50 minutes, then wash with water and soap.
Embodiment 3
[0016] Take a package of yarn, add 2g of dyes AEL Yellow, 27g of AEL Claret, 140g of AEL Zhangqing, add 40kg of water to mix, add 3200g of Yuanmingfen at room temperature, then heat to 40°C, and add after 15 minutes after the temperature reaches 40°C 200g of soda ash, after another 15 minutes, add 60g of caustic soda, wait for 50 minutes, then wash and soap.
[0017] Since this dyeing process adopts the temperature condition of 40°C and uses caustic soda instead of soda ash, this dyeing process not only saves energy consumption, but also saves the cost of auxiliaries, and has less harm to the environment and human health.
[0018] Cost comparison table of new and old process formulas:
[0019]
PUM
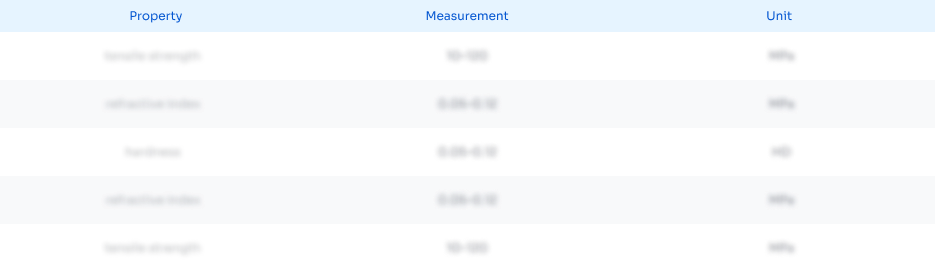
Abstract
Description
Claims
Application Information
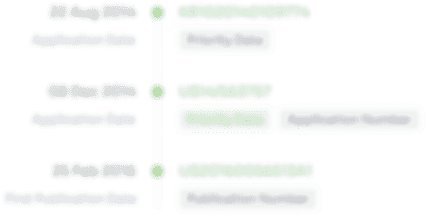
- R&D Engineer
- R&D Manager
- IP Professional
- Industry Leading Data Capabilities
- Powerful AI technology
- Patent DNA Extraction
Browse by: Latest US Patents, China's latest patents, Technical Efficacy Thesaurus, Application Domain, Technology Topic.
© 2024 PatSnap. All rights reserved.Legal|Privacy policy|Modern Slavery Act Transparency Statement|Sitemap