High-temperature shakeout process applied to large-size martensitic stainless steel cast
A martensitic stainless steel and casting technology, which is applied in the field of high temperature boxing process, can solve the problems of occupation, production capacity limitation, and production efficiency decline of foundry factories, so as to improve production efficiency, prevent temperature difference stress and deformation, and reduce direct temperature difference. Effect
- Summary
- Abstract
- Description
- Claims
- Application Information
AI Technical Summary
Benefits of technology
Problems solved by technology
Method used
Image
Examples
Embodiment Construction
[0028] This embodiment takes the casting process of the lower ring of the Three Gorges 700MW class as an example. The material of the lower ring is ZG06Cr13Ni4Mo martensitic stainless steel. The high-temperature boxing process applied to large martensitic stainless steel castings is as follows:
[0029] (1) Using conventional computer simulation methods, calculate the temperature field and stress-strain field of large martensitic stainless steel castings during the cooling process in the sand box;
[0030] In this embodiment, the specific process of calculating the temperature field of the large martensitic stainless steel casting in the sand box cooling process is as follows: based on the Procast casting finite element simulation software, the temperature field of the lower ring during the casting process is calculated, and the lower ring is first extracted. The temperature field at the end of pouring is used as the initial value for the calculation of the temperature field durin
PUM
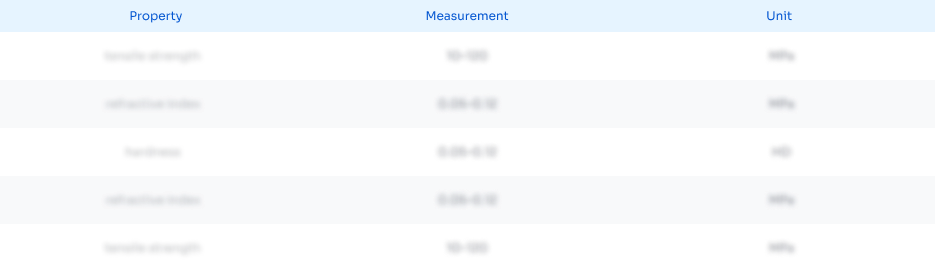
Abstract
Description
Claims
Application Information
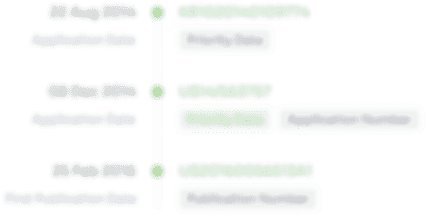
- R&D Engineer
- R&D Manager
- IP Professional
- Industry Leading Data Capabilities
- Powerful AI technology
- Patent DNA Extraction
Browse by: Latest US Patents, China's latest patents, Technical Efficacy Thesaurus, Application Domain, Technology Topic.
© 2024 PatSnap. All rights reserved.Legal|Privacy policy|Modern Slavery Act Transparency Statement|Sitemap