LED vertical chip structure and manufacturing method
A technology of chip structure and manufacturing method, applied in electrical components, circuits, semiconductor devices, etc., can solve the problems of low yield and complex LED chip manufacturing process, and achieve the effects of high yield, uniform current distribution, and large light-emitting area
- Summary
- Abstract
- Description
- Claims
- Application Information
AI Technical Summary
Benefits of technology
Problems solved by technology
Method used
Image
Examples
Embodiment Construction
[0020] The present invention is described in further detail below in conjunction with accompanying drawing:
[0021] refer to figure 1 , LED vertical chip structure described in the present invention is provided with substrate, graphene layer, ZnO nano wall / GaN, n-GaN layer, InGaN / GaN multiple quantum well and p-GaN successively from bottom to top, and described substrate is One of Si, SiC, CuW and Mo, the thickness of the substrate is 20-500 μm, the thickness of the graphene layer is 1-10 layers of graphene, and the thickness of the ZnO nanowall / GaN layer is 2-500 μm. 5 μm.
[0022] Correspondingly, refer to figure 2 , LED vertical chip manufacturing method of the present invention, comprises the following steps:
[0023] 1) On a silicon substrate, SiO with a thickness of 300nm is formed by diffusion furnace oxidation 2 , and then electron beam evaporation on SiO 2 Ni-coated silicon substrate with a thickness of 300nm can be obtained on the layer;
[0024] 2) Put th
PUM
Property | Measurement | Unit |
---|---|---|
Thickness | aaaaa | aaaaa |
Thickness | aaaaa | aaaaa |
Abstract
Description
Claims
Application Information
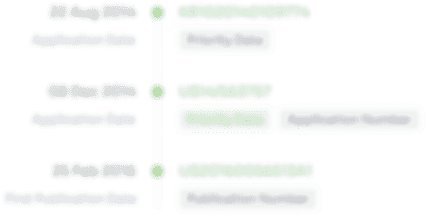
- R&D Engineer
- R&D Manager
- IP Professional
- Industry Leading Data Capabilities
- Powerful AI technology
- Patent DNA Extraction
Browse by: Latest US Patents, China's latest patents, Technical Efficacy Thesaurus, Application Domain, Technology Topic.
© 2024 PatSnap. All rights reserved.Legal|Privacy policy|Modern Slavery Act Transparency Statement|Sitemap